Qualitätssicherung umgeformter Blechbauteile
Alle Ergebnisse auf einen Blick
In der industriellen Fertigung erzielen automatisierte Messverfahren einen hohen Durchsatz bei großer Prozesssicherheit. Das veranlasst vor allem Unternehmen aus dem Bereich Automobilzulieferung dazu, auf automatisierte optische Messsysteme zu setzen. Auf diese Weise lassen sich kürzere Produktzyklen bei gleichzeitig steigenden Stückzahlen erreichen, was wiederum für kürzere Projektlaufzeiten sorgt.
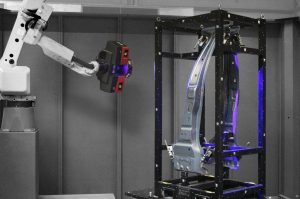
Der Triple Scan Sensor, Kern der Atos Scanbox, ermöglicht die präzise Messung von reflektierenden Blechteilen sowie scharfkantigen Merkmalen wie Laserbeschnitt und Lochbild. (Bild: GOM GmbH)
Die Nachfrage der Automobilzulieferung nach Blechteilen auf hohem Qualitätsniveau wird sich weiter beschleunigen, da auch die Ansprüche an Funktionalität und Sicherheit der Bauteile weiter zunehmen. Um diesen Marktanforderungen gerecht zu werden, setzt der Zulieferer Metalsa auf automatisierte Bauteilinspektion. Das Unternehmen fertigt vor allem Fahrwerksmodule, Karosseriestrukturen sowie Sicherheitssysteme. Zum Kundenkreis des Zulieferers gehören neben deutschen Automobilherstellern wie Daimler, Volkswagen, BMW und Audi auch internationale Marken wie Skoda, Volvo oder Toyota. Um den Kundenansprüchen an Qualität und hohen Stückzahlen gerecht zu werden, setzt das Unternehmen seit 2013 für die serienmäßige Qualitätskontrolle eine schlüsselfertige Plug&Play-Messzelle von GOM ein. Dadurch ist es möglich, die Inspektion der Blechteile automatisiert ablaufen zu lassen, wodurch sich Zeit und Kosten einsparen lassen. Das Unternehmen setzt die automatisierte Messzelle neben dem Werkzeugbau vor allem für die Serienkontrolle ein. Blechteile wie Front Ends, B-Säulen oder Sicherheitskomponenten wie Überrollbügel werden automatisch und optisch gemessen. „Die Zeiteinsparung gegenüber der taktilen Messung ist ein großer Vorteil“, erklärt Marcus Girndt, Leiter der Qualitätstechnik bei Metalsa.
Form- und Maßanalyse von Blechbauteilen
Die Qualitätskontrolle der abgepressten Bauteile vollzieht sich in einem zweistufigen bzw. bei Zusammenbauten in einem dreistufigen Prozess. Nachdem die warmgeformten Bauteile aus der Presse gefallen sind, werden sie das erste Mal vollflächig in der Atos Scanbox gemessen. „In diesem ersten Schritt geht es darum, Form und Abmaße fertigungsnah zu kontrollieren“, erklärt Girndt. Das Teil ist dann zwar geformt, besitzt aber noch keine weiteren Merkmale. Diese erhält es erst beim Laserbeschnitt. „Wir messen die Teile vor dem Beschnitt das erste Mal in Serie, um sicherzustellen, dass wir keine Teile weiterverarbeiten, die die gewünschten Maße nicht einhalten.“ Die vollflächigen Messergebnisse werden bei dieser ersten Messung gegen den CAD-Datensatz kontrolliert. „Das macht die Atos Scanbox automatisch“, führt Girndt aus. Dabei werden neben den Flächenabweichungen zum CAD auch die Form- und Lagetoleranzen abgeleitet. Wenn der Messplan einmal als Vorlage in der zugehörigen Software gespeichert ist, laufen sowohl Messung als auch Inspektion automatisiert ab. Die Messaufnahmen für die gefertigten Bauteile sind dafür mit einem Barcode versehen. Er wird über einen Barcode-Scanner eingelesen, woraufhin die Messzelle den gesamten Messablauf sowie den Prüfbericht selbstständig abspielt. Für die Inspektion der Oberfläche wird das Bauteil dabei virtuell ausgerichtet. Da Bohrungen und Beschnittkanten noch nicht vorhanden sind, zieht die Software markante Formbereiche als Referenz heran. Anhand dieser lässt sich das Bauteil dann virtuell ausrichten. Das ermöglicht die Formanalyse der Teile noch vor dem Laserbeschnitt. „Das würde taktil bei unseren Stückzahlen überhaupt nicht funktionieren“, erklärt Girndt. „Bei einer B-Säule sind für die Formanalyse bis zu tausend Messpunkte zu messen. Das entspricht ungefähr 60 Seiten Prüfbericht. Stattdessen verwenden wir nun die bildhafte Auswertung, die über einen Farbplot auf einen Blick aussagekräftig ist – und sparen mit der optischen Messung zwei Drittel der Zeit ein.“
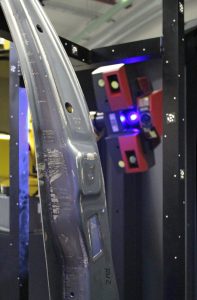
Durch die automatisierte Messung lassen sich Durchlaufzeiten verkürzen und so ein höherer Durchsatz generieren. (Bild: GOM GmbH)
Kontrolle von Lochpositionen und Konturschnitt
Wenn die Form des Bauteiles dem tolerierten Bereich entspricht, geht es mit dem Laserschneiden weiter. Das Bauteil erhält dabei charakteristische Merkmale wie Löcher und Konturschnitt. Anschließend erfolgt eine zweite Messung, bei der nicht mehr die Geometrie, sondern der Laserbeschnitt kontrolliert wird. Lochlage, Beschnitt der Löcher sowie die vollständige Außenkontur des Bauteiles werden dabei mit einer Genauigkeit im 10mm-Bereich geprüft. Je nach Anforderung erfolgt die Auswertung anhand konkreter Messpunkte oder als bildhafte Darstellung. Abweichungen zum CAD-Modell werden dabei farbig gekennzeichnet und in Form von Fähnchen oder Tabellen entnommen.
Zusammenbauanalyse und Trendermittlung
Entsprechen die gefertigten Einzelkomponenten dem Toleranzbereich, gehen sie entweder direkt zum Kunden oder sie werden zur Weiterverarbeitung in den Zusammenbau gebracht. Die optische Messmaschine prüft anschließend ebenfalls die zusammengeschweißten Teile. Flächen- und Beschnittpunkte sowie Lochlagen werden bei den zusammengebauten Komponenten serienmäßig kontrolliert. „Wir wollen vor allem wissen, ob das komplette Teil nach dem Zusammenfügen noch immer passt und ob die Formgenauigkeit weiterhin gegeben ist“, erklärt Girndt. Darüber hinaus führt Metalsa Trendanalysen mit der Messmaschine durch. Dabei werden mehrere Messungen zueinander verglichen und ein Werteverlauf ermittelt. „Wir nutzen diese Funktion beispielsweise bei der Fertigung von B-Säulen. Diese werden bei uns auf zwei verschiedenen Schweißanlagen gefertigt, müssen aber trotzdem exakt dieselbe Form aufweisen.“ Durch die Trendanalyse erkennen die Messtechniker, ob auf einer der beiden Anlagen beispielsweise Verschleiß entsteht, der ggf. zu fehlerhaften Teilen führt.
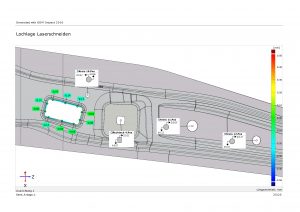
Nach dem Laserschnitt verläuft die Inspektion von Lochbild und Beschnittkanten automatisiert. (Bild: GOM GmbH)
Einfache Bedienbarkeit als Vorteil
Die einfache und intuitive Bedienung der Messmaschine führt dazu, dass auch Mitarbeiter ohne messtechnische Vorkenntnisse in der Lage sind, die Anlage zu bedienen. Mitarbeiter aus der Produktion beispielsweise können die Anlage nach einer halben Stunde Einweisung handhaben. „Das ist ein großer Pluspunkt, wenn man bedenkt, dass wir in kontinuierlichen Schichten produzieren und eigentlich ununterbrochen messen müssen, um die hohe Stückzahl zu bewältigen“, erklärt Girndt. Da sämtliche gemessenen Datensätze automatisch gespeichert werden, lassen sie sich für Trennprojekte jederzeit erneut aufrufen und weiterverarbeiten. „Ungeachtet, welche Informationen wir für andere Projekte brauchen – ein zweites Aufspannen des Teils ist nicht nötig, da wir vollflächige Daten aus allen Messungen haben.“ Zusammenfassend schließt der Messtechniker ab, dass es vor allem drei Aspekte sind, die die Anlage mit Blick auf den Wettbewerb als richtige Investition ausgewiesen haben: die hohe Benutzerfreundlichkeit, die deutliche zeitliche Einsparung sowie die vollflächigen Ergebnisse der optischen Messung.