Automatisierte Fertigung von Faserverbund-Leichtbaustrukturen
Flechtkern statt Sand, Wachs oder Metall
Stand der Technik in der Fertigung von Faserverbund-Leichtbaustrukturen war bisher die Verwendung von Sand, Wachs oder Metalllegierungen, die nicht nur kosten- und energieintensiv herauszulösen sind, sondern teilweise auch zu hohen Umweltbelastungen führen. Munich Composites erreicht nun eine Verbesserung der Verfahren durch eine neuartige Flechttechnik und den Einsatz von kooperierenden Robotern.
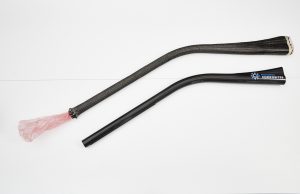
Durch einen neuen Herstellungsprozess werden Faserverbund-Leichtbaustrukturen, wie Feld-Hockeyschläger, jetzt von Robotern geflochten. (Bild: Munich Composites GmbH)
So lässt sich eine verbesserte Faserablage der Carbonfasern realisieren, wodurch sich das Potential der teuren Fasern besser ausnutzen und Prozessabfälle vermeiden lassen. Komplexe Hohlbauteile aus CFK sind in vielen Bereichen der Industrie nötig. Neben der Sport- und Freizeit- sowie Luftfahrindustrie kommen sie vor allem aufgrund von steigenden Umweltanforderungen verstärkt in der Automobilindustrie zum Einsatz.
Die Technik und deren Grenzen
Bisher erfolgte die Fertigung von Hohlprofilen mit der Halbschalentechnik im Prepreg-Verfahren. Hier wurden mit Harz vorgetränkte Matten in die entsprechende Form gelegt und dann unter Druck und Hitze ausgehärtet. Diese Technik hat mehrere Nachteile: Es entsteht hoher Verschnitt, da die spätere Bauteilform aus den Matten auszuschneiden ist. In manchen Fällen kommt es entweder zur Faltenbildung oder es gibt keinen Faserverlauf entsprechend der Kontur des späteren Bauteils, da das Prepreg-Material bei Krümmungen des Bauteils nicht in der Lage ist, den Bauteilverlauf ideal abzubilden. Um trotzdem die benötigten Lasten zu tragen, ist es daher notwendig, mehr Material einzusetzen, als bei idealem Faserablauf nötig wäre. Das führt zu zusätzlichem Gewicht und zu höheren Kosten. In einigen Fällen ist es zudem erforderlich, dass die Faserablage manuell erfolgt. Dabei besteht das Risiko von menschlichen Fehlern, wenn Faserlagen nicht wie geplant eingelegt werden. Schon kleine Winkelabweichungen haben negative Auswirkungen auf die Bauteileigenschaften und damit die Sicherheit des späteren Bauteils. Bei der Flechttechnik hingegen ist nur ein Kern nötig.
Funktionsprinzip und Aufbau
Das Flechtverfahren verfügt über folgende Vorteile gegenüber dem Prepreg-Verfahren: Der Verschnitt ist gering, da direkt über den formgebenden Kern geflochten und nur am Anfang und Ende etwas Material (<5 Prozent) abgeschnitten wird. Das Material des Flechtkerns ist zudem kostengünstiger als Prepreg-Material, da es noch nicht mit Harz getränkt ist. Beim Flechten erfolgt die Faserablage direkt auf den formgebenden Kern. Dabei fährt der Roboter genau die Kontur des späteren Bauteils nach. Somit legen sich die Fasern exakt an der Kontur des Bauteils ab, es entstehen keine Falten und es ist kein zusätzliches Material für Verstärkungen nötig. Die Faserablage lässt sich komplett automatisieren. Drei Roboter führen dabei den Flechtkern durch die Maschine. Damit sind menschliche Fehlerquellen ausgeschlossen und jedes Bauteil weist eine gleichbleibende Qualität und damit gleichbleibende Sicherheitsstandards auf. Der direkt wiederverwendbare Flechtkern ermöglicht auch Hinterschnitte. Denn er besteht aus einem Elastomer und ist schon in der Form des späteren Bauteils hergestellt. Zum Flechten wird der Kern mit Druckluft versetzt und automatisiert überflochten. Danach lässt er sich noch vor der Injizierung des Harzes entnehmen und direkt wieder zum Überflechten verwenden. Hierdurch verbleibt der Kern nicht im späteren Bauteil und schafft damit kein zusätzliches Gewicht. Die Prozesszeit sinkt, da sich der Kern schnell entnehmen lässt. Der Kern lässt sich hunderte Male wieder verwenden und ist somit pro Bauteil günstig in der Herstellung.