Roboter fertigen Antriebe für Aufzüge
Leichter zum Lift
Weltweit entstehen immer mehr und immer größere Städte. Weil geeignetes Bauland knapp ist, werden dem Aufbau funktionierender Infrastrukturen enge Grenzen gesetzt. Die Alternative lautet vertikales Wachstum – und das erfordert vor allem Aufzugsysteme mit energieeffizienten Antrieben. Bei deren Herstellung beschleunigen Roboter die Prozesse und entlasten gleichzeitig die Werker.
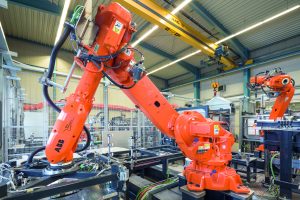
Roboter vom Typ IRB 6640 übernehmen das Handling der Montagehilfen und stellen diese dem Werker bereit zum Bestücken mit Magneten. (Bild: ABB Automation GmbH)
Aktuellen Angaben zufolge wächst die Weltbevölkerung derzeit um mehr als 80Mio. pro Jahr. Parallel zum Bevölkerungswachstum steigt auch die Urbanisierung. Das bedeutet: immer mehr Menschen leben in immer mehr Städten und die Metropolen werden immer größer. Menschen und Waren effizient von A nach B zu befördern ist für Stadtplaner und Architekten zu einer großen Herausforderung geworden. Beim Thema urbane Mobilität denken die meisten Menschen zunächst an den Straßenverkehr sowie an ober- und unterirdisch verlegte schienengebundene Verkehrssysteme. Doch innerhalb von Gebäuden geben andere Transportmittel den Ton an, ohne die keine moderne Großstadt funktioniert: Fahrtreppen, Fahrsteige und vor allem Aufzüge. Aktuellen Schätzungen zufolge befördern die weltweit rund zwölf Millionen installierten Aufzugsanlagen täglich weit über eine Milliarde Menschen, was sie einem der meistgenutzten Transportmittel macht.
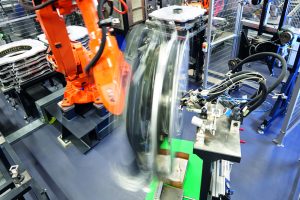
Roboter mit schnell drehender Montagehilfe beim Auftragen des Klebstoffes auf die in der Montagehilfe eingelegten Magnetschalen (Bild: Thyssenkrupp AG)
Robotergestützte Klebe- und Montageanlage
Seine Positionierung im Markt verdankt der Geschäftsbereich Aufzüge des Thyssenkrupp-Konzerns hohen Qualitätsstandards, moderner Technik und intelligenten Aufzugslösungen wie dem Twin-Konzept. Letzteres steht für die weltweit erste Aufzugsanlage mit zwei voneinander unabhängig fahrenden Kabinen in einem gemeinsamen Schacht. Eine intelligente Steuerung sorgt dafür, dass die beiden Kabinen sich die Fahrten über die Stockwerke so aufteilen, dass die Fahrgäste mit jeder Kabine jeweils nur eine Teilstrecke zurücklegen. Sie sind zwar gezwungen umzusteigen, haben dadurch aber insgesamt geringere Wartezeiten, als bei nur einer Kabine pro Schacht. Bauherren wiederum profitieren von einem rund 25 Prozent geringerem Platzbedarf bei gleicher Förderleistung im Vergleich zu konventionellen Aufzugsanlagen. Um jederzeit Produkte hoher Qualität just in time kostengünstig zu produzieren und zu liefern, setzt das Unternehmen auf moderne und hochflexible Fertigungslösungen. Seit Herbst 2014 gehört dazu auch eine vollautomatische, robotergestützte Klebe- und Montageanlage für die Rotoren der Aufzugsmotoren. Den Auftrag über Konzeption, Simulation, Bau und Inbetriebnahme dieser Anlage erhielt die in Unterfranken ansässige Main-Automation. Das auf Roboterautomation spezialisierte Unternehmen entwickelt und realisiert maßgeschneiderte, schlüsselfertige Automationslösungen.
Die Vorteile im Überblick
Ziel der Automation war es, die vielen Varianten an Rotoren für die unterschiedlichen Aufzugsantriebe schneller, präziser und vor allem in einer jederzeit reproduzierbaren Qualität mit Permanentmagneten zu bekleben. Je nach Bauart und Ausführung der Motoren benötigen die Werker in der Montage verschiedene, mit Permanentmagneten bestückte Rotoren. Sie unterscheiden sich in Baulänge und Durchmesser sowie in Anzahl und Anordnung der aufzubringenden Permanentmagnete. Letztere sind dabei je nach Spezifikation in mehreren Lagen mit unterschiedlicher Anzahl an Magneten richtig gepolt zu bestücken. Dauerte das manuelle Bekleben der Rotoren mit Permanentmagneten je nach Motorgröße noch mehrere Stunden pro Rotor, so ist mit der neuen Anlage aufgrund robotergestützter Automation nur noch ein Bruchteil davon erforderlich – und das bei erhöhter Prozess- bzw. Fertigungssicherheit. Dafür sorgt die automatisierte Rotortyp-Identifikation zu Prozessbeginn, die der Anlage mitteilt, welche Vorrichtungen, Stoff- oder Materialmengen, Applikationsprogramme und Verarbeitungszeiten für den jeweiligen Rotor zu wählen sind. All diese Daten sind in einer Bibliothek des Steuerungsprogrammes hinterlegt, wodurch Bedien- oder Programmierfehler durch den Mitarbeiter ausgeschlossen sind. Ein weiterer wichtiger Aspekt für die Automatisierung des Klebeprozesses war der Gesundheitsschutz der Mitarbeiter. Beim manuellen Kleberauftrag mussten sie wegen der gesundheitsgefährdenden Dämpfe Atemschutzmasken tragen und so unter erschwerten Bedingungen arbeiten – das entfällt jetzt.
Anlagen- und Prozessbeschreibung im Detail
Die Anlage besteht aus zwei identischen Bearbeitungslinien. Deren Kernkomponenten sind jeweils ein Applikator für den Kleberauftrag, eine spezielle Fügestation, diverse Montagehilfen zum Aufnehmen und Übertragen der Permanentmagnete sowie zwei ABB-Roboter vom Typ IRB 6640 zur Handhabung der Rotoren und Montagehilfen. Weiter integriert sind Reinigungs- und Lackierstationen sowie am Ende der beiden Linien ein auf einer Linearachse verfahrbar montierter IRB 6650S, der die fertigen Rotoren auf die Lagerplätze verteilt. Der Montageprozess selbst beginnt mit dem manuellen Reinigen der aus der Vorproduktion kommenden, gedrehten Rotoren. Dieser Reinigungsschritt erfolgt deshalb noch manuell, weil das im Vergleich zu Automaten immer noch kostengünstiger und aufgrund der taktilen Fähigkeiten des Menschen präziser und effizienter ist. Die so gereinigten Rotoren gelangen über ein Förderband in die Anlage. Hier vermisst der erste IRB 6640 die Rotornaben mittels eines an seinem Handflansch montierten Laserscanners hinsichtlich Höhe und Durchmesser. Weiter prüft er die Lage der Bohrungsnut, um diese beim Einspannen in einem Dreibackenfutter zu berücksichtigen. Anschließend vergleicht das Programm die Messwerte mit den in der Bibliothek hinterlegten Daten. Die Identifikation durch den Roboter ist sicher, schnell und schließt durch Menschen verursachte Fehlmessungen aus. Aufgrund dieser Daten weiß das System, um welche Leistungsklasse es sich bei dem jeweiligen Motor handelt und welche Magnetbelegung er benötigt. Im nächsten Schritt nimmt derselbe Roboter mit seinem Greifer den Rotor an dessen Innenbohrung auf und setzt ihn zunächst in eine spezielle Aktivierungsanlage und danach in die Fügevorrichtung. Nahezu zeitgleich kommt der zweite IRB 6640 zum Einsatz. Er entnimmt die für den zu bearbeitenden Rotortyp passende Montagehilfe aus einem Depot und stellt sie auf einem gesonderten Förderband für den Werker ab. Dieser legt jetzt manuell die erforderlichen Permanentmagnete in die Aufnahmen der Montagehilfe. Hat der Werker alle Magnete eingelegt, setzt der zweite Roboter die fertig bestückte Montagehilfe in die Applikator- bzw. Klebestation. Diese überprüft zunächst, ob alle Magnete korrekt ausgerichtet und eingesetzt sind. Ist alles in Ordnung, erfolgt die Freigabe für den Klebstoffauftrag. Dazu bewegt der Roboter die zu klebenden Teile entlang einer Dosieranlage, welche die Magnete mit Kleber versieht. Für die Qualität, Festigkeit und Korrosionsbeständigkeit der Klebung sind viele Faktoren ausschlaggebend. Dazu gehören u.a. das korrekte Applizieren des Klebstoffes, die richtige Klebstoffmenge sowie die korrekte Luftfeuchte und Temperatur. Nach vollendetem Kleberauftrag setzt der zweite Roboter die so vorbereitete Montagehilfe in die Fügevorrichtung. Die wiederum fährt den darin bereits befindlichen Rotor in die vorgesehene Fügeposition. Ist diese erreicht, führt die Montagehilfe alle Magnete gleichzeitig von außen auf den Rotor zu. Nach einer bestimmten Haltezeit kommt wieder der erste Roboter ins Spiel. Er setzt den fertig geklebten Rotor in eine Reinigungsanlage. Anschließend setzt er den gesäuberten Rotor noch in eine vollautomatische Versiegelungsanlage zum Lackieren, bevor er ihn auf ein Förderband zum Ausschleusen aus der Klebelinie stellt.
Zwischenstopp im Rotorenlager
Am Ende der beiden Klebelinien übernimmt ein auf einer Linearachse verfahrbar montierter IRB 6650S die fertigen Rotoren und setzt sie in das Rotorenlager. Letzteres arbeitet nach dem Prinzip chaotischer Systeme. Das heißt, der Roboter schaut zuerst nach, wo im Lager ein leerer Platz vorhanden ist, und lagert den Rotor dann dort ein. Letzterer bleibt hier für eine definierte Zeit zum Aushärten des Klebers. Erst danach erfolgt eine Freigabe zur weiteren Bearbeitung (Motoreinbau) an den Werker. Dazu schleust das System den benötigten Rotor über eine kleine Förderstrecke nach dem First-in-First-Out-Prinzip aus dem Lager.