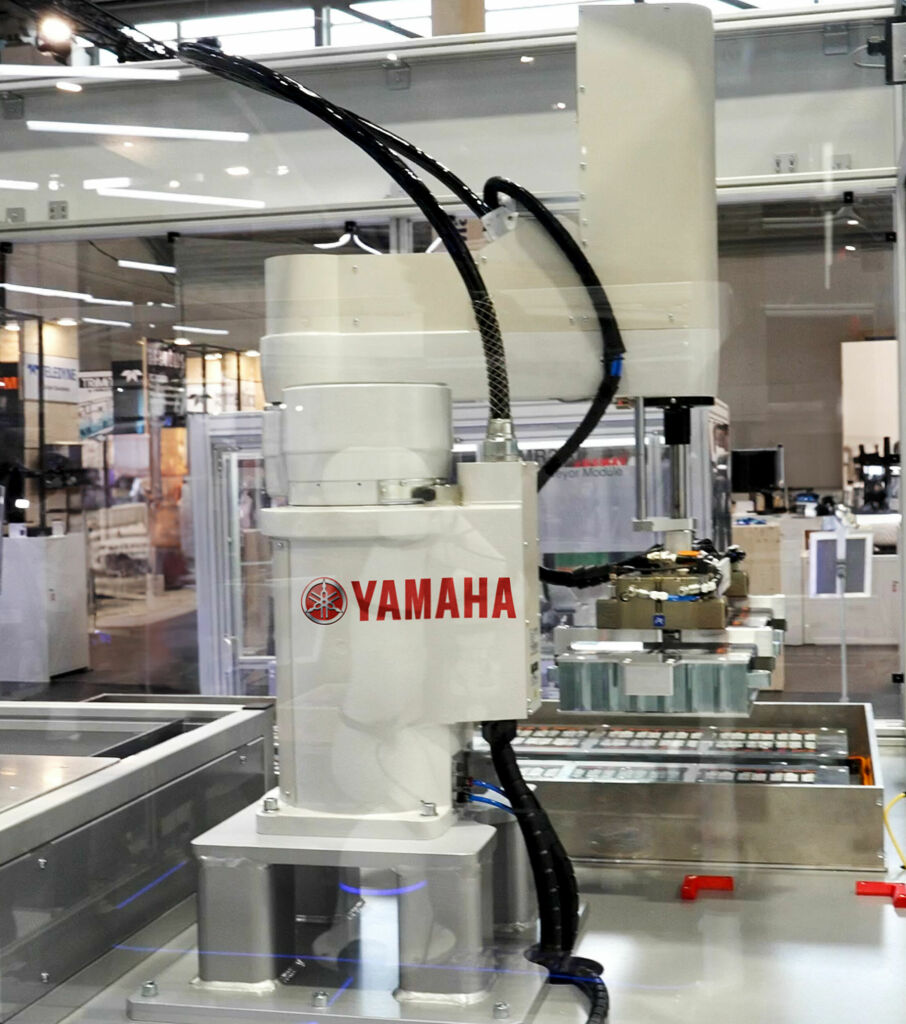
Neue Batteriefabriken entstehen, um die wachsende Nachfrage nach Großbatterien zu bedienen. Der Bedarf kommt nicht nur von der Automobilindustrie, sondern auch von anderen Projekten im Bereich umweltfreundlichen Energiemanagements – wie der energienetzgekoppelten Speicherung. Die Automatisierung der gesamten Prozesskette von Anfang bis Ende steht im Einklang mit den Zielen der Batteriehersteller, Stückzahlen zu erhöhen, Skalierungsvorteile zu nutzen und Wiederholbarkeit zu gewährleisten, die zu gleichbleibend hoher Qualität führt. Darüber hinaus ist es notwendig, Batteriekapazität und Leistungsdaten, wie z.B. Reichweite, zu erhöhen. Nicht zuletzt ist die Produktqualität entscheidend für die Sicherheit der Batterie.
Die Fabriken sind oft riesig, um die Stückzahlen der großen Energiespeicher in kontinuierlicher Produktion zu bewältigen. Fahrerlose Transportsysteme werden in großem Umfang eingesetzt, um schwere Materialien und Komponenten über lange Strecken zu transportieren, während Roboter in großem Umfang eingesetzt werden, um Prozesse, wie die Vorbereitung der aktiven Komponenten, das Anbringen von Elektroden, den Zusammenbau der Zellen und die Herstellung von Modulen und Batteriepaketen, zu bewältigen.
Da die Zellen zu Modulen kombiniert und die Module zu Batteriepaketen zusammengebaut werden, besteht der Produktionsprozess in der Regel darin, Komponenten zu entnehmen und sie präzise zu platzieren, sodass die elektrischen Anschlüsse hinzugefügt werden können. Das kann manuell oder mit Hilfe automatisierter Systeme geschehen.
Schnelligkeit und Präzision bei der End-of-Line-Prüfung
Mit jeder weiteren Prozessstufe werden die Baugruppen größer und schwerer. Ein komplettes prismatisches EV-Batteriemodul kann 30 bis 40kg wiegen, was die Prozessingenieure vor die Herausforderung stellt, die Handhabung, Prüfung und Verpackung dieser Module am Ende der Batterieproduktionslinie zu automatisieren. Eine exakte Platzierung ist bei der End-of-Line-Prüfung äußerst wichtig, um die Modulanschlüsse genau auf die elektrischen Anschlüsse der Prüfvorrichtung auszurichten. Auch der anschließende Transfer des Moduls von der Prüfvorrichtung in das Akkupack, wo die endgültigen elektrischen Verbindungen vorgenommen werden, erfordert eine hohe Genauigkeit. Auch Schnelligkeit ist von entscheidender Bedeutung, um eine hohe Produktivität sicherzustellen.
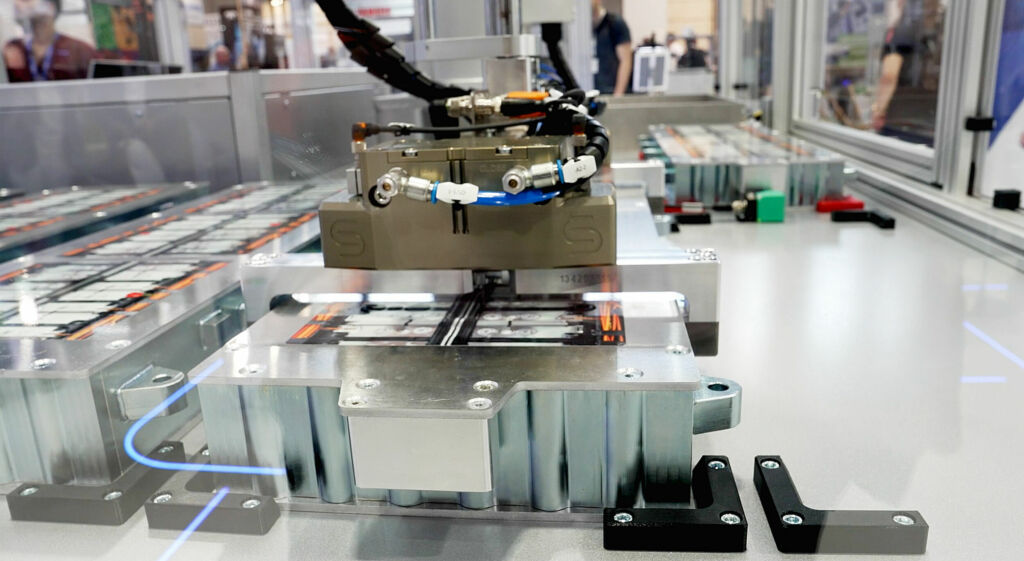
Automatisierung mit Scara-Robotern
Der Markt bietet Scara-Roboter, die eine hohe Tragfähigkeit mit einer präzisionsgesteuerten Hochgeschwindigkeitsbewegung kombinieren, die Gegenstände in der x-y-Ebene mit einer Genauigkeit von 50µm und in der z-Achse mit einer Genauigkeit von 20µm positionieren können. Diese können eine kostengünstige, technisch ausgereifte Lösung für das Bewegen und Positionieren großer, schwerer Batteriekomponenten, wie prismatische Lithium-Ionen-Zellen, bieten. Ein Beispiel hierfür ist Yamahas Serie YK1200X. Die Standard-Scara-Roboter bieten eine Traglast bis 50kg und können Gegenstände mit einer Geschwindigkeit bis 7,5m/s in der x-y-Achse bewegen.
Die Scara-Roboter kamen u.a. bei der Entwicklung des Heavy Exact Rapid Operator (Hero) zum Einsatz, eine Lösung zur Handhabung prismatischer Batteriemodule, die eine vollständige Automatisierung der End-of-Line-Prüfung und -Montage von Batteriepaketen ermöglicht. Die Roboter können dabei die 35kg schweren Module mit hoher Geschwindigkeit und Genauigkeit anheben, bewegen und positionieren. Der Hebemechanismus greift in jeden der vier Hebepunkte an der Außenseite des Modulgehäuses ein und ermöglicht es, das Modul sicher anzuheben, zu bewegen und gegebenenfalls um bis zu 360° zu drehen, um die richtige Positionierung und Ausrichtung sicherzustellen.
Module mit bestandener Prüfung werden aus der Prüfvorrichtung entnommen und in ihre endgültige Position im Batteriepaket transportiert, wo sie bereit sind für die elektrische Verdrahtung und die Endmontage des Batteriepakets.
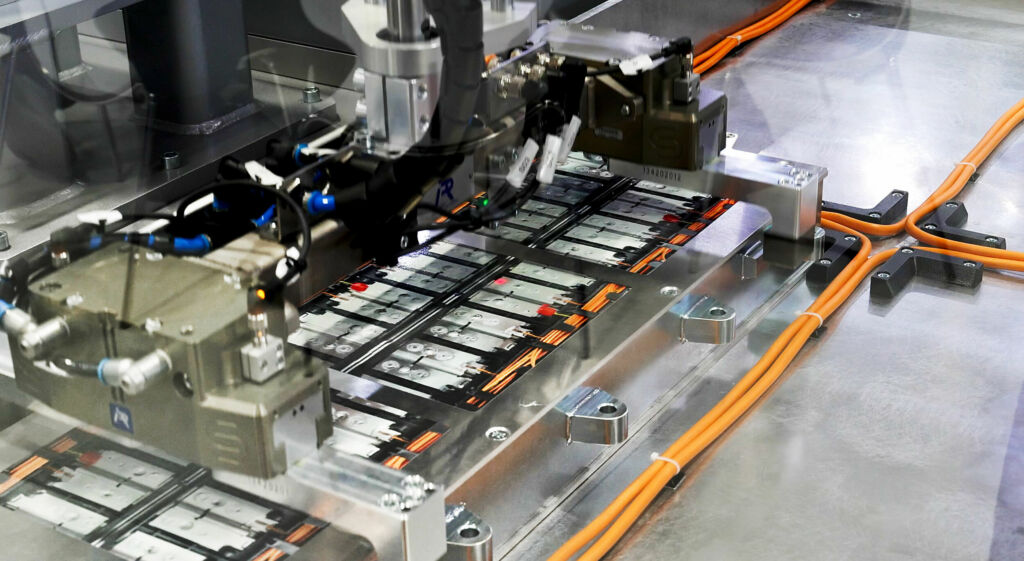
Die Anforderungen an die End-of-Line-Automatisierung können zwischen verschiedenen Batterieherstellern, Batteriepaketdesigns und Fahrzeugtypen erheblich variieren. Die Module müssen unter Umständen präzise in Bezug auf die elektrischen Anschlussstifte einer Prüfvorrichtung oder im endgültigen Batteriepaket positioniert werden. Menschen sind nach wie vor für den Einbau von Leiterplatten, wie dem Batterie-Managementsystem (BMS), die Installation von Kabeln und elektrischen Anschlüssen sowie das Verschließen und Abdichten des Batteriegehäuses in der Endmontagephase zuständig. Eine Scara-basierte Automatisierung kann aber jeden dieser Ansätze unterstützen.
Geringer Flächenbedarf
Unter Nutzung der großen Reichweite des YK1200X, der eine Armlänge von 1,2m aufweist, zeigt die Handling-Lösung, wie alle Batteriemodule, die die elektrischen Tests nicht bestehen, vom Batterie-Fertigungsprozess isoliert und für weitere Untersuchungen oder Reparaturen in einen separaten Bereich gebracht werden können. Während die erweiterte Reichweite die Flexibilität bietet, die Module zu drei verschiedenen Orten zu bringen, um sie zu testen, zu montieren oder zu reparieren, ermöglicht es die Scara-Kinematik, das auf sehr kompakter Fläche zu bewerkstelligen, die nur wenige m2 einnimmt. Eine große Batteriefabrik kann bei Bedarf mehrere solcher Montagezellen integrieren und weitere hinzufügen, um das Produktionsvolumen zu erhöhen.