MRK in der Roboterproduktion
Wenn Roboter Roboter bauen
In den Jahren 2013 und 2014 stiegen die weltweiten Vertriebszahlen für Roboter zur Montageautomatisierung um 10 Prozent auf 24.000 verkaufte Einheiten. Eine der Hauptursachen für diesen Anstieg liegt darin, dass kollaborierende Roboter es ermöglichen, immer mehr Aufgaben zu automatisieren, die sich bislang nur durch manuelle Arbeit lösen ließen. Hersteller können die Cobots nach einer erfolgreich durchgeführten Risikobeurteilung in ihre Produktion integrieren, wo sie als effektive Werkzeuge zum Einsatz kommen.
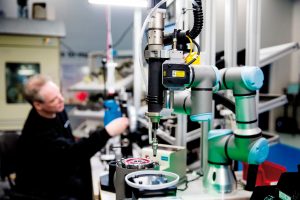
Der kollaborierende Roboterarm UR3 arbeitet nach einer erfolgreich abgeschlossenen Risikobeurteilung ohne oder nur mit geringer Schutzumhausung unmittelbar neben den Mitarbeitern. (Bild: Universal Robots A/S)
Bis zum Jahr 2015 war der Produktionsaufbau der dänischen Firma Universal Robots stark durch Handarbeit geprägt. Doch mit einer seit 2010 jährlichen Verdoppelung der Produktion wurde deutlich, dass diese Lösung nicht mehr länger haltbar ist. „Unser Ziel ist es, die Kosten unserer Produktion in den nächsten drei Jahren um 30 Prozent zu senken. Doch neben dem Preis sind auch wettbewerbsfähige Lieferzeiten ein wichtiger Parameter auf dem Markt. Obwohl wir bereits eine der branchenweit durchschnittlich kürzesten Fristen haben, konzentrieren wir uns weiterhin auf die Verbesserung unserer Produktion. Wir erleben einen explosionsartigen Anstieg in der Nachfrage nach unseren Produkten. Deshalb möchten wir zeigen, dass wir imstande sind, unsere Fertigung entsprechend zu skalieren“, sagt Troels Hornsved, Direktor Supply Chain bei Universal Robots.
Roboter bauen Roboter
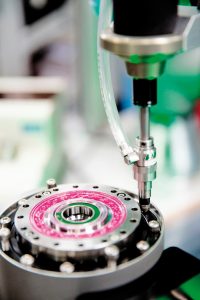
Vier der UR3-Roboterarme leisten seit 2015 Präzisionsarbeit in der Montage von Universal Robots und schrauben die Gelenke für ihre Geschwister der Serien UR3, UR5 und UR10 zusammen. (Bild: Universal Robots A/S)
Insgesamt werden bei der Herstellung eines UR-Roboterarms rund 400 Schrauben verbaut. Allein für die Montage von nur einem der sechs Gelenke jedes Armes sind 28 Schrauben nötig. Besonders die manuellen Schraubprozesse bei der Gelenkmontage kosteten viel Arbeitszeit, weshalb das Unternehmen sich dazu entschied, sich wiederholende Aufgaben an seine eigenen Produkte abzugeben. 2015 fasste die Firmenleitung den Entschluss, eine schlankere Produktion mit identischen Fertigungslinien und getaktetem Betrieb zu implementieren. Heute arbeiten vier UR3-Roboter Seite an Seite mit den Mitarbeitern und montieren die Robotergelenke für die Roboter UR3, UR5 und UR10. „Unsere Roboter sind auch für uns als Hersteller nützlich, wenn es um sich ständig wiederholende Aufgaben geht“, sagt Kurt Hansen, Betriebsingenieur bei Universal Robots. Die Automatisierung der Schraubaufgaben spart nicht nur Zeit in der Produktion, sondern erlaubt auch eine gleichbleibende Qualität der Produkte, stärkt den Produktionsablauf und verbessert das Arbeitsumfeld. Somit sorgt die Mensch-Roboter-Kollaboration auch beim Roboterhersteller selbst für bessere Arbeitsbedingungen. So hatte sich die Installation der vier Montageroboter nach einem Jahr bereits amortisiert.
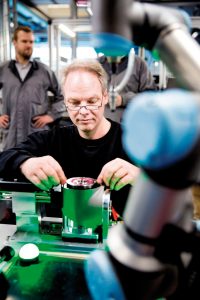
Nachdem der Arbeiter einige Bauteile manuell in das Gelenk montiert hat, drückt er auf seinem Touchpad auf Start und der Roboter übernimmt das Festschrauben der neuen Gelenkteile. (Bild: Universal Robots A/S)
In wenigen Schritten zum fertigen Gelenk
In der Fertigung sind die Roboter auf vier identischen Montagelinien direkt auf den Arbeitstischen installiert. Dort erledigen sie alle Schraubaufgaben für die Montage von Getriebe und Flansch in den Gelenken, aus denen jeder Roboterarm aufgebaut ist. Jedes Gelenk setzt sich wiederum aus einem Gehäuse, einem Getriebe, einem Motor und einem Encoder zusammen. Für ihre Aufgaben sind die Roboter jeweils mit einem integrierten Schraubendreher, einem Laser-Messgerät und zwei Schraubenförderern ausgestattet, die für die Montage von Getriebe und Flansch je zwei unterschiedliche Sorten von Schrauben enthalten. Im Betrieb folgt jeder Roboter einem rotierenden Getrieberad und nimmt in der Bewegung die jeweils benötigten Schrauben selbstständig auf, setzt sie ein und schraubt sie schließlich fest. In der Montage befestigen die Roboter mittels ihres Schraubendrehers zunächst das Getriebe mit zwölf Schrauben im Inneren des Gelenkgehäuses. Das Getriebezentrum des Montageroboters steuert ihn während dieses Schrittes um die eigene Achse, damit keine eventuellen Späne in das offene Getriebe fallen. Ist dieser Prozess abgeschlossen, gibt das Touchpad, das den Roboter steuert, dem Mitarbeiter am Arbeitstisch über ein Signal Bescheid. Der Arbeiter bringt daraufhin den Ring aus Kunststoff, den Flansch und die Spindel des Getriebes manuell im Gelenk an. Anschließend drückt er auf dem Bildschirm des Touchpads auf Start und der Roboter übernimmt wieder die weitere Montage: Er führt Messungen durch, holt neue Schrauben und bringt den Flansch mit 16 Schrauben in einem genau definierten Kreuzmuster an, sodass das Getriebe korrekt zentriert ist. Es ist erforderlich, dass die Getriebeteile und der Flanschausgang exakt zentriert zueinander stehen, da das Getriebe sich im späteren Betrieb ständig dreht und unter Spannung steht. Den Einbau dieser insgesamt 28 Schrauben je Robotergelenk schafft der Roboter in etwa vier Minuten. Währenddessen hat der Monteur am Arbeitstisch Zeit, das nächste Gelenk zur Montage vorzubereiten.
Mit den eigenen Robotern in die Zukunft
Beim Implementieren der Robotertechnik in der eigenen Produktion ging es Universal Robots nicht nur darum, seine Mitarbeiter vor belastenden Aufgaben zu schützen. Das Unternehmen hat damit vor allem auch eine nachhaltige Lösung zum Verbessern seiner Produktionsabläufe geschaffen. Hornsved fasst zusammen: „Der Einsatz der Roboter soll sicherstellen, dass Material und Maschinen sich in unserer Montage mit einem Maximum an Effizienz einsetzen lassen und unsere Produktion ohne Unterbrechungen und Engpässe abläuft. Dadurch, dass wir die zeitaufwendigen Schraubarbeiten bei der Gelenkmontage automatisiert haben, setzen wir die Möglichkeiten unserer kollaborierenden Roboter bestmöglich für uns ein. Mitarbeiter und Roboter arbeiten auf einer Ebene zusammen, anstatt dass die Roboter abseits in einer Ecke stehen. Das macht die Mensch-Roboter-Kollaboration letztendlich aus: Roboter kommen für diejenigen Aufgaben zum Einsatz, in denen sie gut sind – wie sich wiederholende oder körperlich belastende Aufgaben – und wir Menschen tun das, in dem wir gut sind – wie kreative und abwechslungsreiche Arbeiten. Genau darin sehen wir die Zukunft und wir gehen davon aus, dass wir künftig noch mehr Roboter in unseren Produktionslinien einsetzen werden.“