Schlanke Produktionslogistik für Maschinenbauer
Lean auf ganzer Linie
Moderne Intralogistiksysteme befördern heute nicht nur Materialien oder Werkstücke, sondern bahnen auch den Einstieg in eine neue Fertigungskultur. Für Branchen, die – wie der Maschinen- und Werkzeugbau – bisher überwiegend in Standplatzmontage produzieren, bringt eine Umstellung auf Taktfertigung erhebliche Effizienzgewinne. Schienensysteme mit Rundführung bieten eine wirtschaftliche Alternative zu aufwendigen Förderkonstruktionen.

Mit geeigneter Förderlogistik lassen sich selbst schwere Bauteile wie Flugzeugturbinen mit Methoden der Fließfertigung produzieren. (Bild: © terimakasih0/pixabay)
Wo schwere, sperrige Bauteile, Maschinen oder Industriegüter in material- und arbeitsintensiven Fertigungsschritten hergestellt werden, hat die verbreitete Fließfertigung bisher nur zögerlich Einzug gehalten. Viele Maschinen- und Werkzeugbauer scheuen eine Umstrukturierung ihrer Fertigungsabläufe, da den potenziellen Produktivitätssteigerungen vermeintlich hohe Investitions- und Betriebskosten entgegenstehen. Gängige Fördersysteme wie Hallenkräne, Luftgleitkissen oder konventionelle Schienenkonstruktionen sind zumeist kostspielig, aufwendig zu installieren, wartungs- und energieintensiv. Dies erschwert die Abkehr von der traditionellen Insel- oder Standplatzmontage zugunsten einer nach Methoden der Fließfertigung organisierten Produktionslogistik, die auch bei kleinen und mittleren Stückzahlen Vorteile bietet.
Weiter im Takt
Mit dem passenden Logistikkonzept zahlt sich die Einführung einer stationenbezogenen Taktfertigung auch bei Taktzeiten von Stunden oder Tagen aus. Statt alle Montagearbeiten an einem Standplatz durchzuführen, werden die Bearbeitungsschritte auf einzelne Stationen verteilt, die das Erzeugnis in festgelegter Taktung bis zu seiner Fertigstellung durchläuft. Das verschlankt den Fertigungsprozess und steigert die Wertschöpfung, weil sich bei geringerem Platzbedarf, schnelleren Durchlaufzeiten und einem erhöhten Durchsatz die Produktions-, Betriebs- und Lagerhaltungskosten verringern. Aufgrund durchgängiger Transparenz von Produktionsabläufen und Materialfluss erübrigen sich Pufferzeiten, auftretende Fehler und Engpässe lassen sich sofort erkennen und beheben. Die verbesserte Auslastung von Personal und Betriebsmitteln verschafft langfristige Planungssicherheit bei hoher Liefertreue.
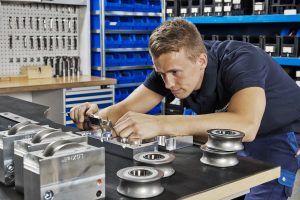
Aufgrund des speziellen Schienen- und Rollenprofils lassen sich tonnenschwere Bauteile ohne Hilfsantrieb von Hand bewegen. (Bild: Losyco GmbH)
Fertigungsvorteile
Zu den Pluspunkten der Fließ- oder Taktfertigung zählt die vereinfachte Strukturierung von Arbeitsabläufen. Indem sich für jede Station die einzelnen Montageschritte präzise takten lassen, bleibt der gesamte Fertigungsprozess fortlaufend im Fluss. Die gleichmäßige Auslastung der Mitarbeiter sorgt für verkürzte Fertigungszeiten, weil die Arbeitsschritte nahtlos ineinander greifen, ohne kostspielige Leerzeiten zu verursachen. Ein weiterer Vorteil ergibt sich bei der Ausrüstung der Arbeitsstätten. Wenn sich schwere Bauteile wie Maschinen oder Bearbeitungszentren im One-Piece-Flow-Verfahren von einer Station zur nächsten bewegen lassen, sind nicht mehr an jeder Montagestation alle Spezialwerkzeuge, Materialien und Medien vorrätig zu halten. Die präzise Zuordnung der verschiedenen Arbeitsschritte zu den jeweiligen Stationen ermöglicht es, die Montagebereiche den ergonomischen Anforderungen anzupassen, indem beispielsweise Übergabe-, Hebe- und Senkvorrichtungen genau dort installiert werden, wo sie im Fertigungsprozess erforderlich sind.
Präzise Planung
Viel Kapital wird dadurch gebunden, dass Materialien vorzuhalten und Lagerbestände zu verwalten sind. In diesem Bereich zahlt sich die Umstellung auf Taktmontage ebenfalls häufig aus. Aufgrund der stationenbezogenen Logistik lässt sich genau bestimmen, wieviele Bauteile und Materialien wann an welcher Station benötigt werden. Das macht es möglich, die Taktung bis auf die Zulieferketten auszudehnen, um den Bedarf just in time zu decken und damit Bestände und Lagerhaltung zu reduzieren. Auf Kundenseite stellt die geregelte Taktung eine beschleunigte und termingerechte Auftragsabwicklung sicher. Durch die langfristige Planbarkeit von Durchlaufzeiten und Ausstoß weiß das Unternehmen jederzeit, wann welches Auftragsvolumen abgewickelt wird und sorgt damit für hohe Zuverlässigkeit und Liefertreue.
Schlanke Logistiklösung
Im Werkzeug- und Maschinenbau ist die Einführung der Taktfertigung mit besonderen Herausforderungen verbunden. Zu den zentralen Aspekten zählt die Wahl des geeigneten Fördersystems, mit dem sich selbst schwergewichtige Lasten sicher und wirtschaftlich von Station zu Station bewegen lassen. Neben den Investitions- und Betriebskosten muss auch der Installationsaufwand überschaubar bleiben, damit die Fertigungsumstellung ohne lange Ausfallzeiten vonstatten geht. „Viele unserer Kunden stehen anfangs vor der Frage, welche Lösung ihren Anforderungen am besten entspricht“, berichtet Manuel Granz, Vertriebsleiter der Losyco GmbH. „Deshalb haben wir mit der Loxrail ein System entwickelt, das auf die speziellen Erfordernisse dieser Branchen zugeschnitten ist.“ Im Unterschied zu herkömmlichen Förderschienen, deren Räder durch ihre Spurkränze einen erheblichen Reibungskoeffizienten aufweisen, fällt der Rollwiderstand bei dem System ausgesprochen gering aus. Selbst tonnenschwere Bauteile lassen sich ohne Hilfsantrieb von Hand bewegen und präzise positionieren. Zudem bietet diese Fördertechnik Montagevorteile gegenüber vergleichbaren Lösungen, weil die Führungswellen mit nur einer Fixierleiste fest im Aluminiumprofil verankert sind. Die verbesserte Klemmwirkung wirkt Längsverschiebungen der Führungswelle im Profil entgegen.
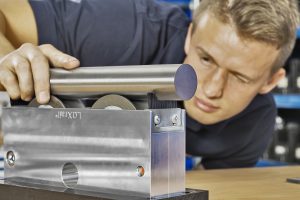
Das Schienensystem verhilft zu klar strukturierten Fertigungsabläufen bei planungssicherem Durchsatz. (Bild: Losyco GmbH)
Schwerlast leicht bewegen
Das System ist in zwei Größen mit hoch belastbaren, geschliffenen und gehärteten Führungswellen in Durchmessern von 25 und 40mm lieferbar. Es schließt Radsätze für verschiedene Traglasten, Standard- und Schwerlast-Transportwagen sowie unterschiedliche Antriebskonzepte ein. Die Standardwagen sind für Traglasten bis 40t ausgelegt, wobei die Nenntraglasten mit der Zahl der Radsätze variieren. In getakteten Montagelinien mit One-Piece-Flow lassen sich die Transportmittel als mobile Arbeitsstationen nutzen. Das schnell installierte Schienensystem eignet sich zur Nachrüstung in bestehenden Werkshallen. Für den Einbau werden mit einem Betonschneider Schlitze gefräst und die eingesetzten Schienen anschließend fugendicht vergossen. Da das Aushärten des Mörtels nur wenige Stunden beansprucht, ist die Loxrail schon nach kurzer Zeit betriebsbereit. Sämtliche Umbauarbeiten können an einem Wochenende erfolgen, ohne dass es zu Produktionsausfällen kommt. Die flurebene Installation verhindert, dass Stolperfallen oder Rillen entstehen. Weil die Oberkante der Führungswellen nur wenige Millimeter über den Hallenboden herausragt, stellt die Schiene kein Hindernis für Mitarbeiter, Flurförderfahrzeuge, Rollregale oder Reinigungsmaschinen dar. Für abzweigende Fertigungslinien sind Kreuzungen und Weichen erhältlich.