3D-Sensor für Inline-Messungen im Karosseriebau
Direktes Feedback aus der Linie
Auf dem Weg zur Losgröße 1 müssen Karosseriebauer schon heute eine wachsende Variantenvielfalt auf ein und derselben Produktionslinie bewältigen. Dies erfordert immer kürzere Anlaufzeiten für den Produktionsprozess und eine gleichbleibend hohe Prozesssicherheit trotz kurzfristiger Anpassungen. Genau auf diese Anwendungen ist der optische 3D-Sensor Aimax Cloud zugeschnitten.
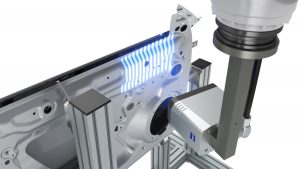
Der Streifenlichtsensor Animax Cloud nimmt innerhalb von ca. einer halben Sekunde ein digitales Abbild einer Werkstückkomponente auf und ermöglicht so ein unmittelbares Feedback aus der Produktionslinie. (Bild: Carl Zeiss Automated Inspection GmbH & Co. KG)
Drei Ziele standen für Dr. Kai-Udo Modrich, Geschäftsführer, und Michael Scheffler, Business Development Manager bei der Carl Zeiss Automated Inspection bei der Entwicklung ihres neuen Sensors im Vordergrund: Erstens sollte der roboterbasierte Inline-Sensor dazu beitragen, die Anlaufzeiten für neue Produktionsanlagen zu reduzieren. Zweitens galt es, in der laufenden Serienproduktion Trends bei den Messwerten in Echtzeit erkennbar zu machen, um die Prozesse rechtzeitig optimieren zu können, im Idealfall noch bevor Produktionsfehler auftreten. Laut Scheffler wird dies zunehmend wichtiger: „Der schnelle Variantenwechsel kann in Zukunft bedeuten, dass keine Zeit bleibt, den Verbau einer Kombination von Bauteilen vorher zu testen.“ Die Prozesssicherheit könne somit nur mit flexiblen Fertigungs- und Prüfsystemen gewährleistet werden sowie mit kurzfristigen Prozessanpassungen im Fertigungstakt. Und drittens verfolgte das Team um Modrich und Scheffler das Ziel, mit dem neuen Sensor auftretende Fehler unmittelbar zu identifizieren. So sollen fehlerhafte Bauteile sofort aussortiert bzw. Nacharbeiten zugeführt werden. Im Extremfall kann die Produktion frühzeitig gestoppt werden. Ergänzend zu dieser Zielsetzung hatte der neue Sensor den wachsenden Anforderungen neuer Fahrzeugstrukturen im Leichtbau und Multimaterialmixe genauso gerecht zu werden wie zusätzlichen Messmerkmalen infolge aktueller Fertigungstechnologien. Das Ergebnis dieser Entwicklungsleistung ist der optische 3D-Sensor Aimax Cloud.
100 Prozent-Messung im Fertigungsstakt
Eine 100 Prozent-Messung im Fertigungsstakt hat nicht zuletzt in der Anlaufphase einer neuen Produktionsanlage einen entscheidenden Vorteil gegenüber Stichprobenprüfungen: Sie bietet ein unmittelbares Feedback, wie sich Parameteränderungen, z.B. bei den Schweißrobotern, auf die Bauteilqualität auswirken. Dafür nimmt der Streifenlichtsensor innerhalb von ca. einer halben Sekunde ein digitales Abbild eines Werkstückes auf. Die Ergebnisse der Messungen liegen sofort vor – in Form von Positionsdaten zur Lage und Größe von Merkmalen. Der Sensor muss dazu nicht umständlich justiert werden, sondern erkennt Standardsituationen – z.B. bei der Messung von Bolzen – automatisch, ohne dass der Anwender optische Parameter eingeben muss. So lässt er sich rasch in Betrieb nehmen – ideal für minimale Anlaufprozesse. Erreicht werden konnten die kurzen Mess- und Inbetriebnahmezeiten durch ein ausgeklügeltes Zusammenspiel aus Sensorik, Datenvorverarbeitung und -auswertung. Neben den kurzen Messzeiten war eine Voraussetzung für den Einsatz in der Inline-Messtechnik des Karosseriebaus auch die kompakte Bauform. „Radkästen, Tunnelbereiche, Fenster – in solche Karosseriebereiche gelangt nur ein kleiner, kompakter Sensor crashfrei“, erläutert Scheffler. Dafür mussten die Entwickler u.a. die Projektionstechnik des Sensors entsprechend anpassen – mit dem Resultat, dass er jetzt mit Maßen von 145x168x96mm problemlos in enge Innenbereiche gelangt.
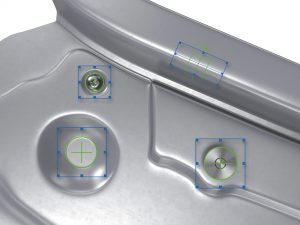
Mit dem AlMax Cloud lassen sich aus einem Bild auch Auswertungen mehrerer Merkmale ziehen. (Bild: Carl Zeiss Automated Insection GmbH & Co. KG)
Neue Merkmale und Materialien messen
Weiterentwicklungen im Automobilbau bringen neue, komplexe Messmerkmale mit sich. Beispiele sind Sitz, Position und Winkligkeit von Nieten, die im Zuge neuer Verbindungstechnologien zum Einsatz kommen. Diese waren bislang nicht prüfbar, weil die Informationsdichte der vorhandenen optischen Sensoren dazu nicht ausreichte. Fünflinienprojektionen beispielsweise projizierten lediglich ein statisches Gitter auf ein Bauteil. Der neue Sensor erfasst die Oberfläche von Werkstücken dagegen dreidimensional in Form von Punktwolken. In Kombination mit den speziell entwickelten Algorithmen der Software misst der Sensor somit selbst Merkmale, die bislang zumindest im Fertigungstakt nicht messbar waren. Ein weiterer Vorteil der hohen Informationsdichte: Während bisher jedes einzelne Messmerkmal separat erfasst werden musste, lassen sich jetzt aus einem Bild auch Auswertungen mehrerer Merkmale ziehen. Das beschleunigt die Messung zusätzlich. Nicht nur gegenüber neuen, komplexen Messfeatures, auch angesichts der zunehmenden Materialvielfalt zeigt der Inline-Sensor eine hohe Flexibilität. Die diversen Werkstoffe – von Aluminium über hochfeste Stähle bis zu kohlenstofffaserverstärkten Kunststoffen – erfordern eine Optik, die sich deren unterschiedlicher Oberflächeneigenschaften anpasst. Eine adaptive Beleuchtung regelt Intensitäten und Farben je nach Bedarf und erzeugt selbst an Materialübergängen präzise Messwerte. Modrich: „Eine moderne, smarte Produktion im Karosseriebau lässt sich heute in Anlauf und Serienbetrieb nur effizient gestalten, wenn sie durch eine zeitgemäße Inline-Messtechnik unterstützt wird“.