Roboterschweißen im Nutzfahrzeugbau
Sichere Nähte bei großen Bauteilen
Die landwirtschaftlichen Geräte der Claas-Unternehmensgruppe verrichten ihren Dienst auf den Feldern weltweit. Bis die Maschinen jedoch auf dem Acker arbeiten, durchlaufen sie eine hochkomplexe Produktionskette. Sicher verschweißt werden die großen Bauteile dabei seit mehr als 20 Jahren von Robotern. Als die Technik dann doch ausgetauscht werden musste, brachte der neue Partner Panasonic Robot & Welding seinen Roboter TL-2000 WGH3 zur Europapremiere in das Projekt ein.
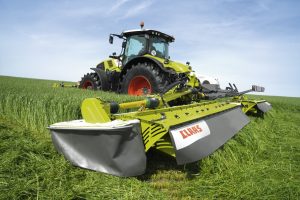
Vom Werk auf das Feld: Class bedient den weltweiten Markt für landwirtschaftliche Geräte. (Bild: Claas KGaA mbHBild: Claas KGaA mbHBild: Panasonic Automotive & Industrial Systems Europe GmbH)
Traktoren, Mähdrescher, Rund- sowie Quaderballenpressen bis hin zur Futterernte – die Claas-Unternehmensgruppe bietet ein umfassendes Produktportfolio für die Landwirtschaft. Bei den selbstfahrenden Feldhäckslern hat der Hersteller nach eigenen Angaben einen Weltmarktanteil von über 50 Prozent. Mit mehr als 100 Jahren seit ihrer Gründung bedient die Unternehmensgruppe einen klar definierten Kundenstamm. Dieser besteht aus sowohl aus klassischen Landwirten als auch großen Lohnunternehmern. „Unser Ziel ist es, bei den Profis unsere Maschinen zu platzieren“, sagt Herr Remensperger, Leiter der Vorfertigung. Um sich im oberen Qualitätssegment dauerhaft zu behaupten, sind eine ausgelastete Wertschöpfungskette und einwandfreie Produkte erforderlich. Um das zu erreichen, verfolgt das Unternehmen die Philosophie, die wichtigsten Prozessschritte bei der Produktherstellung im eigenen Hause durchzuführen: So findet das Roboterschweißen komplexer Baugruppen, deren Lackierung sowie die Endmontage der Produkte stets im eigenen Hause statt. Dabei liegt der Fokus dieser Do-It-Yourself-Strategie nicht nur auf der Qualitätssicherung, sondern insbesondere auf der Sicherheit der Baugruppen.
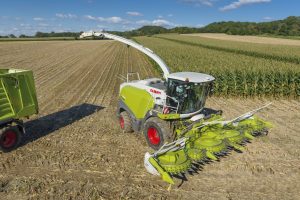
Vom Werk auf das Feld: Class bedient den weltweiten Markt für landwirtschaftliche Geräte. (Bild: Claas KGaA mbHBild: Claas KGaA mbHBild: Panasonic Automotive & Industrial Systems Europe GmbH)
Der Service muss stimmen
Traktoren, Futtererntemaschinen und Co. gehören zu den industriellen Gütern mit sehr aufwendigen Herstellungsprozessen. Besonders die großen Bauteile, die miteinander verschweißt werden, stellen eine Herausforderung dar. Seit 1988 befasst sich Class bereits mit dem Roboterschweißen und ist damit ein Pionier im Nutzen von automatisierten Schweißverfahren. Über 20 Jahre sorgte eine gut bekannte Technik hier für zufriedenstellende Schweißergebnisse. Ab einem gewissen Zeitpunkt war das nicht mehr genug: „Die bestehende Technik entsprach nicht mehr unseren Erwartungen; Wir konnten Defizite in der Schweißnahtverfolgung, beim Antasten der Bauteile und in der Einfachheit der Programmierung feststellen, sodass es für uns Zeit war, uns auf dem Markt umzuschauen und andere Hersteller zu vergleichen,“ schildert Remensperger.
Alles aus einer Hand
Auch wenn das Schweißergebnis den Ansprüchen genügt, fließen weitere kritische Faktoren mit ein, die im letzten Jahrzehnt immens an Bedeutung gewonnen haben: So sind etwa die Zuverlässigkeit der Serviceeinsätze, die Flexibilität der Anlage und zusätzliche Dienstleistungen für den Produzenten von großer Bedeutung. Daher war bei der Wahl des Partners für das neue Roboterschweißen das Serviceangebot eines der wichtigsten Kriterien bei der Anbieterwahl. Schlechte Erfahrungen aus der Vergangenheit galt es zu vermeiden, wie Geschäftsführer Remensperger erläutert: „Wir hatten die Schweißmaschine von einem Hersteller, das Schlauchpaket von einem anderen und der Roboter wurde von einem dritten Hersteller angefertigt – so hatten wir einzelne Komponenten, welche in Einklang gebracht werden mussten.“ So ergab sich bei Qualitäts- und Systemproblemen Verantwortungsdiffusion zwischen den Herstellern. Das Unternehmen wurde nicht selten von einem Ansprechpartner zum nächsten geschickt „Dies ist nicht nur kosten- sondern insbesondere zeitintensiv. Der neue Anbieter musste alles aus einer Hand anbieten können“. Denn Zuschlag erhielt schließlich Panasonic Robot & Welding mit ihrer Tawers-Technologie von , eine Fusion von Roboter, Robotersteuerung, Stromquelle und Servo-Drahtvorschub. Mit diesem System sollten Schnittstellenprobleme ausgeschlossen werden.
Schweißen in großer Reichweite
Um dem Anspruch an die Ergebnisse beim Roboterschweißen bei großen Bauteilen gerecht zu werden, schnitt Panasonic ihre Anlage passgenau auf die Ansprüche des Fertigungsbetriebes zu. So sollte eine Verfahrachse sicherstellen, dass sich die Schweißnähte an der speziellen Bauteilgeometrie gut erreichen lässt. Damit ist es möglich, den Roboter mit geringem Aufwand in die gewünschte Schweißposition zu stellen. Auch der Schweißroboter wurde entlang der spezifischen Anforderungen des Herstellers gewählt: Dabei feierte der Panasonic-Roboter TL-2000 WGH3 seine Europapremiere. Der Roboter ist in der Lage, selbst Schweißprozesse mit großer Reichweite zu bewältigen. Zudem erhöht die Tawers-Technologie Hyper Dip Puls (HD-Puls) die Schweißgeschwindigkeit mit geringer Kerbwirkung und ermöglicht zusätzlich einen kurzen Lichtbogen. Das erhöht die Stabilität und reduziert die Abweichung des Lichtbogens. Jörg Radzei, Key Account Manager von Panasonic sagt: „Was HD-TV für den Fernsehzuschauer ist, ist HD-Puls für den Schweißprozess: Der feine Unterschied!“ Aufgrund der schnellen Verfügbarkeit der Roboter wurde das Schweißsystem zügig in die Wertschöpfungskette von Class implementiert.
Individualisiertes System
Class nutzte das Angebot von Panasonic, ein Schweißkonzept entlang der eigenen Ansprüche zu gestalten. Dabei integrierte der Fertiger das Schweißsystem mit der DTPS Offline-Programmierungs-Software und einer Option zur Nahtverfolgung. Das System soll sich so langfristig an wandelnde Herstellungsprozesse anpassen lassen, ohne jedesmal eine Lösungen erwerben zu müssen. „Nicht nur unsere Produktion konnte mit den Panasonic-Anlagen stabilisiert werden – Unser Output erhöhte sich merklich und auch die Maschinenverfügbarkeit konnte von 84 Prozent auf 86 Prozent gesteigert werden“, sagt Remensperger. Weiter laufen Anlagen homogener und die Anzahl der Spritzer ging zurück.
Fünf Anlagen installiert
Fünf Schweißanlagen wurden im Unternehmen eingerichtet. Es wurden vor drei Jahren drei baugleiche Anlagen erworben, und anschließend ein Folgeauftrag für zwei Anlagen erteilt. Ein Beleg für die fruchtbare Zusammenarbeit der beiden Partner. „Die Projekte werden wirklich ernst genommen“, schildert Remensperger „Es ist zu erkennen, dass Panasonic motiviert ist, den Kunden völlig zufriedenzustellen“.