Interdisziplinäres Forschungsprojekt Robofill 4.0
Flexibel in die Zukunft
Der gesellschaftliche Trend hin zu individualisierten Produkten wächst kontinuierlich und hat längst auch den Markt der Getränkeindustrie erreicht. Was sich im kleinen Rahmen noch händisch realisieren lässt, ist in der Massenfertigung bislang aufgrund von starren Produktionsprozessen undenkbar. Sie verhindern, dass sich kleine Losgrößen flexibel in eine laufende Produktion integrieren lassen. Deshalb bedarf es neuer Abfüllkonzepte, die jederzeit auf neue Aufträge, Geräteausfälle und andere Einflüsse reagieren.
Das interdisziplinäre Forschungsprojekt Robofill 4.0 hat sich die Entwicklung neuer Abfüllkonzepte zum Ziel gesetzt und dafür eine Handvoll etablierter Industrieunternehmen und Forschungsinstitute gewonnen, die nun gemeinsam an der flexiblen Zukunft arbeiten. Egal ob Weihnachten, Geburtstag oder eine Einladung zum Essen: Ein kleines Geschenk kommt immer gut an. Hier entwickelt sich der gesellschaftliche Trend zunehmend weg von einheitlicher Massenware hin zu individualisierten Produkten. Der Endverbraucher will direkten Einfluss auf das bestellte Produkt nehmen, vom selbstgestalteten Logo über den passenden Produktnamen bis hin zu individuell zusammenstellbaren Rezepturen. Die Lieferung soll ohne Umwege über zusätzliche Handelsstufen direkt an den Verbraucher erfolgen. Soweit die Theorie. In der Praxis fiel der Startschuss im Jahr 2003, als das erste deutsche Unternehmen individualisierte Produkte für den Bereich Lebensmittelindustrie anbot. Zehn Jahre später teilten sich laut Fachliteratur bereits 71 Firmen den wachsenden Markt. Solange die Nachfrage noch verhältnismäßig gering ist, lassen sich die Bestellungen manuell bearbeiten. Doch der kontinuierlich steigende Bedarf erfordert für die Zukunft Prozesse, die individuelle Produkte wirtschaftlich rentabel in die Massenfertigung integrieren und so kostendeckend einem großen Markt zur Verfügung stellen. Dafür bieten sich insbesondere flexible Produktionen im Sinne von Industrie 4.0 an – also Produktionen, die nicht durch den Menschen gesteuert werden müssen, sondern die auf Basis einer digitalen Intelligenz autonom handeln und den Menschen nahtlos integrieren.
Aktueller Stand: starre Produktionsprozesse
Aktuell sind Abfüll- und Verpackungsanlagen hoch spezialisiert, damit sie eine möglichst hohe Ausbringung erreichen. Bis zu 80.000 Flaschen pro Stunde schaffen solche Systeme, wobei der Transport der Produkte und Verpackungseinheiten über starr verkettete Produktionslinien erfolgt. Ein Wechsel des zu verarbeitenden Formats oder gar eine individuelle Bearbeitung von Produkten ist nicht vorgesehen. Einzelne Produktionseinheiten lassen sich nicht autark nutzen. Ebenso wenig lassen sie sich ohne erheblichen Aufwand mit Cloud-basierten Diensten verbinden, damit sie gemäß entsprechender Verbraucher-, Prozess- oder Logistikanforderungen individuell agieren können. Diese Ausrichtung zeigt sich sowohl bei den großen Getränkeherstellern als auch bei mittelständischen und kleinen Unternehmen.
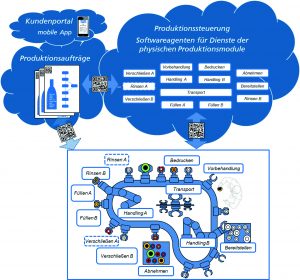
Konzeptübersicht des Projektes Robofill 4.0 mit Zusammenspiel von Kundenportal und Auftragssystem (Bild: Technische Universität München)
Flexible Fertigung mit Robofill 4.0
Der Prototyp einer modernen, modular erweiterbaren und flexiblen Abfüll- und Verpackungsanlage ist das Ziel des derzeit laufenden interdisziplinären Forschungsprojekts Robofill 4.0 – Robotergestützte Abfüllung für die Getränkeindustrie. Das von der Bayerischen Forschungsstiftung geförderte Projekt besteht aus einem Zusammenschluss mehrerer Industrieunternehmen und Forschungsinstitute. Die wissenschaftliche und administrative Koordination erfolgt in kooperativer Zusammenarbeit zwischen dem Fraunhofer IGCV und den an der Technischen Universität München beheimateten Lehrstühlen für Brau- und Getränketechnologie sowie für Lebensmittelverpackungstechnik. Hinzukommen die Firmen Krones, Proleit, Siemens, Till, Yaskawa Europe, Zimmer, Beckhoff Automation, Staatsbrauerei Weihenstephan und Infoteam Software. Das Konzept sieht die direkte Einbindung des Endverbrauchers über ein Online-Kundenportal vor. Von dort aus wird der Auftrag an die Fertigung weitergegeben. Die einzelnen Produktionsmodule, also beispielsweise Rinser, Füller und Verschließer, sind so konzipiert, dass sie autark arbeiten. Besonders herausfordernd ist hier das Schaffen eines flexiblen Füllsystems, das die Produktion von Mischgetränken mit einem vom Endkunden frei wählbaren Mischungsverhältnis ermöglicht. So kann der Verbraucher über das Shop-System sein Biermischgetränk (z.B. Radler) nach seinem persönlichen Geschmack zusammenzustellen und produzieren. Technologische Herausforderungen sind hier insbesondere in den qualitativen Anforderungen an ein verkaufsfähiges Produkt sowie in der Gestaltung eines effizienten Materialflusssystems mit einem Produkthandling auf engstem Raum zu sehen. Das System übernimmt die Aufgaben eines systeminternen Logistikdienstleisters. Dabei ermöglichen spezielle Industrieroboter mit intelligenten Greifsystemen die funktionsspezifische Handhabung an den Bearbeitungsstationen. Die Anlagen- und Steuerungstechnik muss deshalb ebenfalls flexibel gestaltet sein, um auf alle Änderungen des Produktionsumfelds reagieren zu können. Etikettiert werden die Flaschen mit einem speziellen Tintenstrahldrucker, der direkt auf die Flasche druckt.
Industrie-4.0-Technologien nutzen
Als finaler Baustein ermöglicht ein Multiagentensystem die dezentrale und durch das Produkt getriebene Produktion. Zwar existieren Agentensysteme bereits seit über 15 Jahren, doch gerade durch Industrie 4.0 gerät die Technologie als dezentrales Steuerungselement zunehmend in den Fokus. Es entsteht dadurch ein cyberphysisches System (CPS), bestehend aus einer Menge von eingebetteten Systemen, wie beispielsweise Industriesteuerungen, Sensoren und Aktoren, die über eine Kommunikationsinfrastruktur miteinander kommunizieren. Hinzukommen noch die Produkte. Theoretisch lässt sich jede an der Produktion beteiligte physische Komponente als digitaler Schatten in Form eines Software-Agenten abbilden. In der Praxis bietet es sich jedoch an, nur die Komponenten abzubilden, die auch ein Teil der flexiblen Fertigung sind. Jedem dieser Objekte wird über eine eindeutige Kennung ein Agent zugeordnet. Der Agent kennt den aktuellen Zustand des Objekts, der sich aus dem internen Status (z.B. wer bin ich, wo bin ich, was ist bereits mit mir passiert) und den Zielen (z.B. was soll ich machen, wo will ich hin, was soll mit mir passieren) zusammensetzt. Er versucht nun anhand konfigurierbarer Strategien (z.B. möglichst schnell oder ressourcensparend) selbstständig seine Ziele zu erreichen. Dafür kommuniziert er mit seiner Umgebung und anderen Agenten. Je nach System kann dies auch dazu führen, dass hochkomplexe Zielfindungsstrategien realisiert werden. Ein entscheidender Vorteil der virtuellen Intelligenz auf mehreren Agenten gegenüber einer zentralen Steuerung ist: Ausfälle einzelner Komponenten lassen sich dynamisch ausgleichen, indem andere Agenten diese Aufgaben mit übernehmen oder ein anderer Lösungsweg gefunden wird. Die Produktion kann also trotz des Ausfalls eines Teilsystems weitergeführt werden.

Modell eines Multiagentensystems im Fertigungsumfeld: Jede transporteinheit, jede Fertigungseinheit und jedes Werkstück erhält einen eigenen Agenten. (Bild: Infoteam Software AG)
Agenten für einfache und komplexe Objekte
Die künstliche Intelligenz der Agenten spiegelt sich in der Kombination aus Objekt, Zustand und Kommunikation wider. Hierfür gibt es grundsätzlich drei unterschiedliche Möglichkeiten, Objekte und Agenten miteinander zu koppeln – das sogenannte Mapping. Für alle Arten gilt dabei, dass die Zugriffs- und Ausfallsicherheit des Systems auf Agentenebene durchgeführt wird. Dazu gehört die Zustandsspeicherung in Datenbanken zur Ausfallsicherheit und die Systemsicherheit innerhalb des Agenten oder der Sicherheitszone. Komplex aufgebaute Objekte verfügen unter Umständen bereits über eigene Speicher und Prozessoren. Dazu gehören beispielsweise Anlagen, die autark arbeiten müssen. Diese vorhandene IT-Infrastruktur lässt sich nutzen, indem der Softwareagent direkt innerhalb des physischen Objektes gespeichert und ausgeführt wird. Von dort aus tritt er mit den anderen Agenten in Kommunikation. Weniger komplexe Objekte besitzen nur einen integrierten Speicher, einen Flash-Speicher oder einen beschreibbaren RFID-Tag. Dieser Speicher lässt sich in der Produktion mit dem Zustand des Objektes beschreiben, sodass alle Informationen direkt im Objekt gespeichert sind. Der Agent jedoch wird nicht auf dem Objekt ausgeführt, sondern z.B. in einer Cloud, von wo aus er den Zustand des Objektes ausliest und aktualisiert. Für beide beschriebenen Methoden gilt, dass sie beliebig skalierbar, also an die speziellen Bedürfnisse des Anwendungsfalles anpassbar sind. Nimmt man als physische Teilkomponente der Fertigung beispielweise eine speicherprogrammierbare Steuerung innerhalb einer Abfüllanlage, so wird diese sowohl eine Datenhaltung haben, wie auch Funktionalitäten bereitstellen: Hier sind Teile der Intelligenz demnach auch in der Steuerung selbst integriert und lassen sich vom Agenten nutzen. Als mögliche Zugriffsschnittstellen für den Datenaustausch bzw. den Methodenaufruf zwischen Agenten und physischen Objekten kann OPC UA verwendet werden. OPC UA entwickelt sich immer mehr zum Standard für die Übertragung von komplexen Daten in der Automatisierung und wird von modernen Industriesteuerungen unterstützt. Die dritte Möglichkeit für die Verknüpfung zwischen Agenten und Objekten, wie beispielsweise Werkstücken, ist das sogenannte Tagging. Diese Lösung bietet sich besonders für einfach gehaltene Objekte an, wie Getränkeflaschen. Sie müssen nicht mit kostenintensiver Hardware ausgestattet werden, sondern erhalten einen Barcode, QR-Code oder RFID-Tag, der von einem Lesegerät ausgelesen werden kann. So lässt sich jedes Objekt eindeutig identifizieren und dem Software-Agenten zuordnen. Der dazugehörige Agent wird in der Cloud ausgeführt. Der Zustand des Objektes liegt ausschließlich im Agenten und wird auch hier aktualisiert. So lässt sich jedes Werkstück kostengünstig in das Agentensystem integrieren.
Umsetzung des Agentensystems
Für das Forschungsprojekt Robofill wird der Endkunde über ein Onlineportal die individuelle Fertigung seiner Getränkeflasche in Auftrag geben (digitales Ticket). Jede Flasche wird mit einem eindeutigen QR-Code versehen und lässt sich dem Werkstückagenten zuordnen, der in einer Cloud ausgeführt wird. Physischen Modulen des Produktions- und Materialflusssystems werden Agenten zugeordnet, die anhand des digitalen Tickets mit den benötigten Produktionsaufträgen und Produktionswissen versorgt werden. Hierbei lassen sich moderne Abfüll- und Verpackungsanlagen u.a. über die integrierte OPC-UA-Schnittstelle in das Multiagentensystem integrieren. Neben dem Multiagentensystem und dem webbasierten Kundenportal wird die virtuelle Produktionsumgebung noch durch die Auftrags- und Datenverwaltung inklusive eines Datenbanksystems ergänzt.