Roboter übernehmen Bohrplatzieren und Werkzeug-Handling auf Bohrplattformen
Der Alltag eines Arbeiters ist auch auf heutigen Bohrplattformen in der Regel noch manuelle Schwerstarbeit – und sehr gefährlich. Die Technik hat sich über viele Jahrzehnte nur wenig weiterentwickelt. Der Einsatz von Robotern soll das jetzt ändern und Bohrplattformen zu einem sichereren Arbeitsplatz machen.
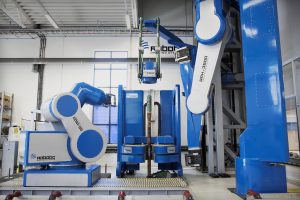
Die Firma RDS hat ein System aus mehreren vollautomatischen Bohrrobotern entwickelt, die selbstständig als Team zusammenarbeiten. (Bild: Robotic Drilling systems AS)
Selbst bei hochmodernen Bohranlagen läuft das Handling des Bohrrohres gegenwärtig höchstens halbautomatisch ab. Sobald es aber um andere Objekte geht, wie beispielsweise die Bohrgarnitur oder die Verkleidung, Werkzeuge oder Komponenten, wird das Handling umständlich und zeitaufwendig, da manuelle Arbeitsschritte und der Austausch des Handling-Equipments nötig sind. Zudem erfordert die Arbeit eine große Anzahl an Arbeitern auf der Bohrplattform, um die großen Maschinen zu bewegen. Eines der Hauptziele der Tätigkeiten der FIrma Robotic Drilling Systems (RDS) ist es, die Menschen aus den gefährlichen Bereichen der Bohrplattformen zu holen. Das Unternehmen hat dazu in den letzten fünf Jahren ein System aus mehreren vollautomatischen Bohrrobotern entwickelt. Es ermöglicht, die normalerweise anstrengenden und gefährlichen Tätigkeiten des Bohrrohrplatzierens und Werkzeug-Handlings schneller und präziser zu erledigen – ohne die Anwesenheit eines Menschen.
Präziser Siebenachser mit 1.500kg Traglast
Um das zu erreichen, hat RDS drei Entwicklungen hervorgebracht: mehrere Bohrplattformmaschinen, wie den Robotic Pipe Handler RPH-3500 oder den Robotic Iron Roughneck RIR-270, die ein flüssiges, vollautomatisches Handling der Bohrrohre und Werkzeuge ermöglichen; ein dynamisches Robotersteuerungssystem, das flexible Operationen erlaubt, und einen Drill-Floor-Roboter, der die manuellen Arbeitsschritte ersetzt. Der Drill-Floor Robot DFR-1500 stellt den zentralen Roboter im System dar. Er greift einzelne Bohrelemente und bringt sie für den Bohrvorgang in Position. Dazu greift er selbstständig auf verschiedene Werkzeuge zu und wechselt sie innerhalb von Sekunden. Dabei ist der Siebenachsroboter nicht nur präzise, sondern gleichzeitig auch sehr leistungsfähig: Seine maximale Traglast liegt bei 1.500kg.

Das Nabtesco-Getriebe verfügt über eine optionale Hohlwelle, die es ermöglicht, Kabel und Leitungen durchzuführen. (Bild: Nabtesco Precision Europe GmbH)
Roboter programmieren sich selbst
Für die Steuerung der Roboter entwickelte das Unternehmen eine eigene Software-Plattform. Sie ermöglicht die nahtlose Zusammenarbeit zwischen den verschiedenen Robotern. Mithilfe der Software lassen diese sich einfach umprogrammieren, wenn das Bohrprogramm kurzfristig geändert werden muss. Der Bediener teilt dem Roboter lediglich mit, welche Aufgabe er erledigen soll und nicht, wie er diese durchzuführen hat. „Der Roboter programmiert sich selbst und arbeitet mit anderen Maschinen bzw. Robotern über ein integriertes Antikollisionssystem zusammen“, erklärt Jimmy Bostrøm, COO Officer von RDS. Das Steuerungssystem erlaubt es den Robotern, autonom oder halbautomatisch bzw. ferngesteuert zu operieren – je nach Bedarf. Das definiert die Rolle des Drillers neu, sodass er sich auf die wichtigen Bohrarbeiten konzentrieren kann, statt auf das Bohrgestänge- und Werkzeug-Handling. Das System ist bei Neuinstallationen wie auch als Nachrüstlösung bei bestehenden Bohranlagen einsetzbar. Untersuchungen zeigen, dass sich mit dem Robotersystem jährlich bis zu 40 Arbeitstage pro Bohranlage einsparen lassen – nicht-produktive Zeit eingerechnet. Tausende manuelle Arbeitsschritte entfallen. Zusätzlich zur Zeitersparnis lässt sich die Arbeitssicherheit erhöhen und die Betriebskosten reduzieren. Das Robotersystem bietet weitere Vorteile wie geringere Stillstandzeiten, schnellere Installation, verringerter Geräuschpegel, niedrigerer Energieverbrauch sowie CO2-Emissionen.
Leistungsfähige Antriebslösungen
Für die Roboter benötigte RDS besonders leistungsfähige Antriebslösungen. „Für uns stellte es sich als großer Vorteil heraus, für die Entwicklung der neuen Roboter Ingenieure eingestellt zu haben, die eine Menge Expertenwissen aus der Robotik mitbrachten. Daher wussten wir genau, welche Anforderungen wir an den Getriebelieferanten und dessen Produkte zu stellen hatten“, so Bostrøm. Bei der Suche nach der passenden Technik fielen die Zykloidgetriebe von Nabtesco auf. „Zum einen arbeiten sie spielfrei und weisen ein hohes Übersetzungsverhältnis auf; zum anderen bietet Nabtesco die Getriebe auch mit Hohlwelle an, die es uns ermöglicht, elektrische Kabel komplett durch die Getriebe hindurchzuführen, was eine hohe Integration erlaubt“, erklärt Bostrøm. Weitere Argumente seien die Wartungsfreiheit, der gute technische Support und die Instandhaltung seitens des Herstellers sowie kurze Lieferzeiten gewesen. Zudem hatten die Ingenieure von RDS bereits bei früheren Tätigkeiten gute Erfahrungen mit den Antriebslösungen und der Zusammenarbeit mit Nabtesco gesammelt.
An die Anwendung angepasst
Nabtesco verfügt über ein breites Portfolio an Zykloidgetrieben mit Voll- oder Hohlwelle, die auf Präzision, Robustheit und Leistungsfähigkeit ausgelegt sind. Konstruktionsbedingt arbeiten die Exzentergetriebe praktisch verschleißfrei und erreichen dadurch eine lange Lebensdauer. Eine wichtige Serviceleistung des Herstellers sind kundenspezifische Änderungen: Die Konstrukteure von Nabtesco entwickeln bei Bedarf für den Kunden anwendungsspezifische Getriebelösungen, die an die individuelle Applikation angepasst sind. Im Bohrplattform-Roboter und im Bohrrohr-Handler sind sechs bzw. vier Nabtesco-Getriebe verbaut. Im elektrischen Bohrarbeiter kommt ebenfalls ein Zykloidgetriebe des Anbieters zum Einsatz. Dabei handelt es sich um Sondergetriebe, die eigens für RDS angepasst wurden.

Die Roboter von RDS erledigen das Bohrplatzieren und das Werkzeug-Handeln schneller und präziser als Menschen. (Bild: Robotic Drilling Systems AS)
Erfolgreicher Robotereinsatz
Robotersysteme des Unternehmens kommen bereits vom Bergbau bis zur Metallindustrie erfolgreich zum Einsatz. Sie lassen sich ohne Probleme in rauen oder lebensunfreundlichen Umgebungen einsetzen, in denen die Arbeit für einen Menschen nur schwer oder gar nicht möglich wäre. In der Fertigungsindustrie werden Roboter bereits seit vielen Jahren in der Produktion eingesetzt; die Öl- und Gas-Industrie war dagegen bisher konservativ eingestellt. Mit dem automatisierten Bohrrobotersystem könnte sich das nun ändern.