Greiferwerkzeug für Deltaroboter
Mit 3D-Druck zur vierfachen Kraft
Manchmal tritt der Kunde mit besonderen Herausforderungen an seinen Lieferanten. Wenn es dann auch noch sehr schnell gehen muss, kommt man mit klassischen Möglichkeiten oft nicht weit. Dann ist zu prüfen, welches Potenzial neue Technologien bieten. So war es auch im folgenden Beispiel: Hier konnte mit den Methoden der additiven Fertigung ein flexibler und leistungsstarker Sauggreifer entwickelt werden, so wie er in der Verpackungslinie benötigt wurde.
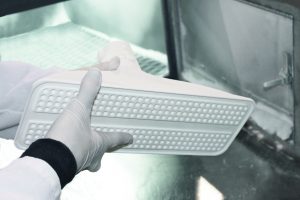
Die Unterseite des Sauggreifers: Es wäre unmöglich gewesen, diese Löcher mit einem konventionellen Verfahren herzustellen. (Bild: Anubis 3D)
Die neuen Pick&Place-Roboter waren bereits bestellt, als die Langen Group, Zulieferer eines großen amerikanischen Lebensmittelherstellers, die Konzeption eines Greiferarmes in Angriff nahm. Mit seiner Hilfe sollten die Roboter abgepackte und gestapelte Cracker greifen und in Kartons verpacken. Doch die Ingenieure stießen auf ein Problem: Der Greifer musste ultraleicht sein. Denn um mit der maximalen Geschwindigkeit des Roboters arbeiten zu können, durfte der Greifer zusammen mit dem Produkt nicht schwerer als 2kg sein. Da die größte Verpackungseinheit bereits 1,5kg auf die Waage brachte, musste das verwendete Endstück also weniger als 500g wiegen.
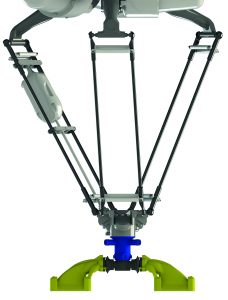
Die vollständige Sauggreifer-Baugruppe, befestigt an einer Parallelkinematik. (Bild: EOS GmbH Electro Optical Systems)
Geringes Gewicht und einfaches Auswechseln im Fokus
Als weltweit tätiger Anbieter von Warenumschlags- und Warenverpackungsausrüstung wandte sich die Langen Group an Anubis 3D, eine Division der Anubis Manufacturing Consultants Corporation mit Sitz im kanadischen Mississauga. „Die Gewichtsbeschränkung schloss Aluminium oder Metallblech als Material aus“, fasst Tharwat Fouad, Präsident bei Anubis, die grundlegende Herausforderung zusammen. „Für einen schwereren Metallgreifer hätten größere Roboter bestellt werden müssen, die teurer gewesen wären – zudem bestand auch noch ein hoher Zeitdruck.“ Darüber hinaus sollte sich das Werkzeug ohne Muttern und Schrauben befestigen lassen, damit das Bedienpersonal die Greifereinheiten einfach und vor allem schnell auswechseln kann. „Es gab insgesamt zwei völlig unterschiedliche Konfigurationen, verschiedene Formen und drei Kartongrößen, wobei jeweils zwei kleine Kartons oder ein großer Karton bestückt werden müssen“, erklärt Fouad. „Der Kunde wünschte sich ein Werkzeug, das sich für alle Kartongrößen eignet.“
Die Wahl der richtigen Fertigungstechnologie
Fouad und sein Team hatten bereits für frühere Kundenprojekte den Markt studiert und wichtige Erkenntnisse über die jeweiligen Fertigungstechnologien gesammelt. „Wir stellten fest, dass Systeme zur additiven Fertigung von Kunststoffen vor allem im Rapid Prototyping verwendet werden“, erklärt Fouad. „Doch unsere Beweggründe waren völlig andere. Wir wollten funktionale Endkomponenten produzieren und waren überzeugt, dass der industrielle 3D-Druck auch dafür die richtige Technologie ist.“ Nachdem die Entscheidung für die additive Fertigung stand, führte Fouad eine detaillierte Analyse der auf dem Markt erhältlichen Fertigungssysteme durch und wählte schließlich das Modell Formiga P 100 aus dem Hause EOS. Innerhalb weniger Tage hatte der Anbieter das System geliefert und in Betrieb genommen. Die Bedienung war relativ einfach zu erlernen. „EOS war dabei immer an unserer Seite“, so Fouad, „und auch heute sind wir mit unserer damaligen Entscheidung noch sehr zufrieden.“ Um die Akzeptanz der additiven Fertigung zu steigern, ist es laut Fouad elementar, jahrzehntealte Denkmuster aufzubrechen. „Es ist möglich, anstelle von Metall Kunststoffe einzusetzen, wenn dies ingenieurswissenschaftlich fundiert erfolgt. Man muss sich auf die Teilegeometrie konzentrieren und die traditionellen Bedenken bezüglich der Komplexität von Bauteilen einfach über Bord werfen. Die EOS-Technik ist diesbezüglich nämlich keinen Einschränkungen unterworfen.“

Zur Herstellung des Greifers setzte Anubis auf die Formiga P100 von EOS, hier in der Abbildung das Nachfolgesystem P110. (Bild: EOS GmbH Electro Optical Systems)
Additive Fertigung im Einsatz
Ebenso wichtig für die Umsetzung der von Fouad angestrebten Endprodukte war die Werkstoffauswahl. Mit EOS-Systemen können beispielsweise hochwertige Polyamide, Polystyrole, thermoplastische Elastomere und Polyaryletherketone verarbeitet werden. „Das System ermöglicht es uns, eine schier endlose Palette an Bauteilen aus gängigen Werkstoffen der Branche zu produzieren“, so Fouad. Dabei arbeitet es mit einem leistungsstarken Laser und Präzisionsoptik, um Bauteile schnell und akkurat zu fertigen. Der Laserstrahl verschmilzt Schicht für Schicht das pulverförmige Kunststoffmaterial und erzeugt so hochkomplexe Teile. Die Vorteile der EOS-Technik zeigten sich schnell. Zu den ersten von Anubis additiv gefertigten Teilen zählte auch ein Greifer für eine Blasformanwendung. Laut Fouad hat diese sein Team inspiriert und belegt, was die additive Fertigung mit Kunststoffen möglich macht. Seitdem hat Anubis verschiedene ähnliche Werkzeuge für Kunden mit Spritzgussanwendungen oder Flaschenverpackungslinien sowie verschiedene Halterungen und Träger entwickelt und sich so als Innovationstreiber in vielen Branchen einen Namen gemacht. Inzwischen hat das Unternehmen zwei weitere EOS-Systeme erworben.
Leicht, flexibel und leistungsstark
Anubis hat seinem Kunden aufgrund der additiven Fertigungsmöglichkeiten eine maßgeschneiderte Lösung für das Projekt präsentieren können. Statt einer traditionellen Metallvakuumplatte mit Luftkanälen – für deren Konzeption und Fertigung mehrere Monate hätten veranschlagt werden müssen – wurden leichtere und abgestimmte Komponenten entwickelt, die die vierfache Greifkraft der Vorgängerbauteile besaßen. Es war nur eine Woche nötig, um das neue Greiferwerkzeug additiv zu fertigen, zusammenzubauen und final auf seine Einsatzfähigkeit zu prüfen. Für das Hauptsaugelement wurde Polyamid 12 verwendet, da es äußerst flexibel ist, Verformungen standhalten kann und für den Lebensmittelkontakt zugelassen wurde. Die Wanddicke des Sauggreifers variierte je nach Abschnitt zwischen 2 und 3,5mm. Die Bauteile wurden mithilfe eines Softwareprogramms, das das Design der Strukturen durch eine Anpassung der Wanddicke an die geforderte Festigkeit bzw. Flexibilität organisch optimiert, speziell für die additive Fertigung konzipiert. „Durch die Effizienz des überarbeiteten Lochprofils wies der Greifer nun eine Saugkraft auf, die sogar das Gewicht einer Bedienperson hätte halten können“, erklärt Fouad. Die Langen Group lieferte die Sauggreifer aus und montierte sie auf den neu eingetroffenen Robotern im Werk des Cracker-Herstellers. „Ein Werkzeug zu entwickeln und herzustellen, das die von uns gewünschten Greifeigenschaften aufweist und dabei noch die Nutzlastbeschränkungen des Roboters berücksichtigt, wäre früher gar nicht möglich gewesen“, sagt Robert Husnik, Engineering Manager bei der Langen Group. „Aufgrund der gestalterischen Freiheit, die uns die additive Fertigung bietet, sind wir nunmehr in der Lage, bisher Unmögliches zu vollbringen.“