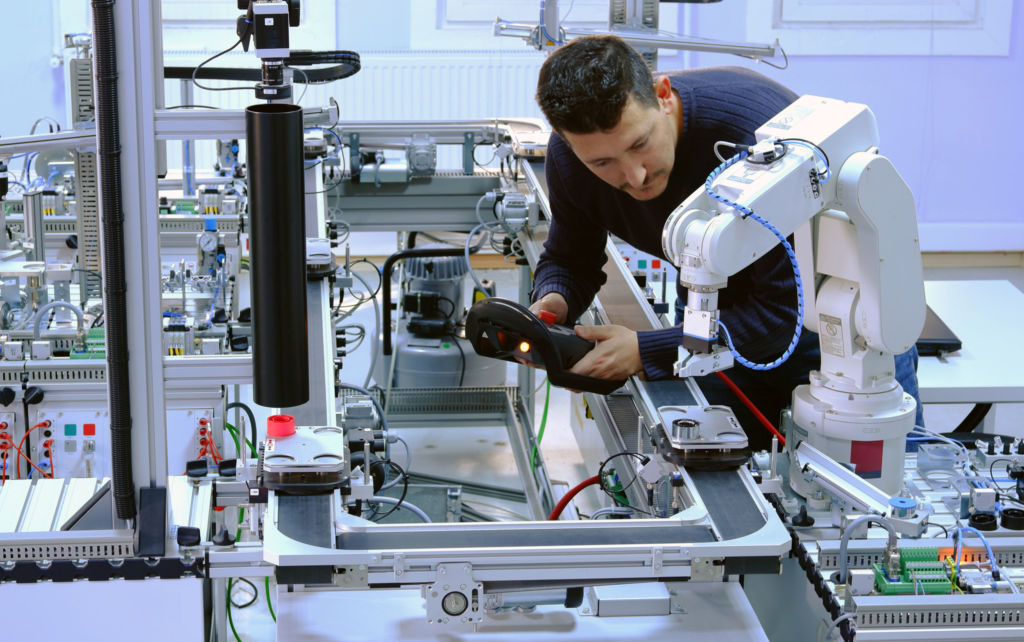
In nicht wenigen Fällen ist die Instandhaltung über den gesamten Lebenszyklus für über 50 Prozent der Anlagenkosten verantwortlich. Daher können angepasste Instandhaltungsprozesse, durch die der Arbeitsaufwand sowie Stillstandzeiten verringert werden, Kosten einsparen. Die Instandhaltung der Anlage lässt sich durch zwei wichtige Maßnahmen verbessern:
- Automatisierung bisher händischer Arbeitsschritte durch die Verwendung von Daten
- Vorbereitung von Arbeitsschritten an der Anlage mittels einem gekoppelten digitalen Zwilling
Mit entsprechenden digitalen Werkzeugen werden diese Verbesserungen ohne Zusatzaufwand erreicht und ergänzen die klassische Instandhaltung ohne mit ihr im Widerspruch zu stehen. Damit kann für jede Situation der bestmögliche Instandhaltungsansatz bzw. -mix eingesetzt werden.
Bei der Instandhaltung von Roboteranlagen werden üblicherweise einzelne Teach-Punkte, das heißt zentrale Wegpunkte des Roboters, korrigiert oder Teile des Roboterprogramms neu vermessen. Auch das Einmessen von Werkzeugen nach einem Wechsel erfolgt direkt an der Anlage. Diese Arbeitsschritte sind häufig iterativ und werden händisch durchgeführt. Die Anpassung des Programmablaufs bzw. der Programmlogik wird dagegen meistens als tieferer Eingriff begriffen.
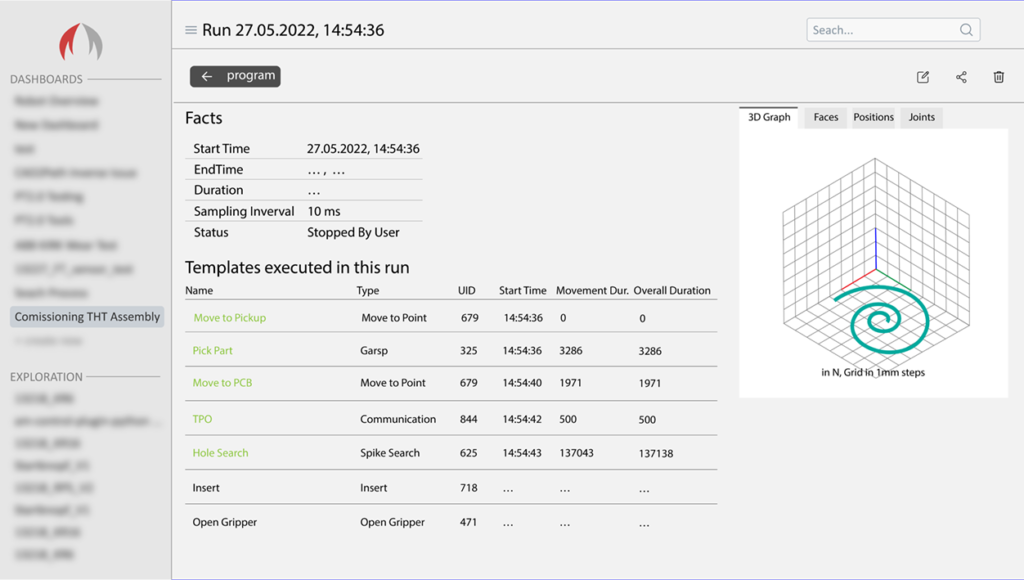
Händische Korrektur von Teach-Punkten
Für die händische Korrektur von Teach-Punkten muss die Produktion gestoppt werden, damit der Instandhalter den Roboter an der Anlage verfahren kann. Bei der Fließfertigung kommt erschwerend hinzu, dass in einem solchen Fall die richtige Produktvariante, für die Korrekturen notwendig sind, in der Anlage zum Stehen kommt. Der Instandhalter führt Korrekturen in mehreren Runden durch, bis der Prozess wieder stabil läuft. Daraus können erheblicher Arbeitsaufwand und lange Stillstandzeiten resultieren. Wenn sowieso Sensorik in der Roboteranlage eingesetzt wird, bietet sich bei häufigen Abweichungen durch wiederkehrende Unregelmäßigkeiten daher die datengetriebene Automatisierung der Anpassung an.
Datengetriebene Automatisierung von Instandhaltungskorrekturen
Adaptive Roboteranlagen setzen 2D-Kameras, 3D-Kameras, Linienlaser oder Kraft/Momenten-Sensoren ein, um sich flexibel an die Produktionsbedingungen anzupassen. Aufgrund der Verfügbarkeit von Sensordaten sind diese besonders für die datengetriebene Automatisierung von Instandhaltungskorrekturen geeignet. Bei jedem Durchlauf einer Roboteraufgabe werden dazu alle relevanten Parameter der Bewegung hochfrequent in einer Datenbank abgespeichert. So können Parameterveränderungen über verschiedene Durchläufe hinweg algorithmisch ausgewertet werden. Das ist etwa für die automatische Korrektur von Teach-Punkten nutzbar. Dabei wird das in den gesammelten Daten repräsentierte tatsächliche Prozessverhalten analysiert, um Teach-Punkte zu berechnen, die die adaptive Roboteraufgabe statistisch schneller und mit weniger Fehlerhandhabung durchführen lassen.
Die datengetriebene Automatisierung von Instandhaltungskorrekturen verringert die Arbeitszeit und ermöglicht darüber hinaus die präzise Berücksichtigung geringer Abweichungen über sehr viele Durchläufe hinweg. Wichtig ist, dass dieser Prozess jederzeit mit manueller Instandhaltung kombinierbar sein muss, da der Mensch in der Lage ist, Ausnahmen zu adressieren, auf die kein Algorithmus vorbereitet ist. So können auch in der Instandhaltung zur Korrektur von Teach-Punkten Mensch und Algorithmus ihre Stärken komplementär ausspielen.
Wird dagegen eine Veränderung der Programmlogik benötigt, ist oft eine manuelle, zeitaufwendige Anpassung notwendig. Diese direkt an der Anlage durchzuführen kann hochgradig ineffizient, unkomfortabel und fehleranfällig sein. Es bietet sich an, diesen Arbeitseinsatz bestmöglich vorzubereiten. Dazu überträgt man das aktuellste Programm – mit allen Änderungen durch bisherige manuelle oder datengetriebene automatische Korrekturen – einfach in eine digitale Engineering-Umgebung, überarbeitet das Programm und spielt es in Folge auf die Anlage zurück. Da die neusten, lokalen Korrekturen permanent einbezogen werden, entsteht so ein einfacher digitaler Zwilling.
Durchgängigkeit der Programmveränderungen
Bei der Verknüpfung der verschiedenen Methoden ist es wichtig, dass die Durchgängigkeit der Programmveränderungen garantiert ist. Das heißt, dass wiederholt händisch an der Anlage angepasste Teach-Punkte von der datengetriebenen Autokorrektur verarbeitet und die Ergebnisse umgekehrt an der Anlage wieder manuell angepasst werden können müssen. Hierfür ist es notwendig, dass beide Veränderungen problemlos in den digitalen Zwilling und auch wieder zurückfließen können. Programmlogik und Daten auf unterschiedliche Datenverarbeitungssystemen, wie Robotersteuerung, SPS, Industrie-PC an der Linie und Engineering-PC im Büro oder geteiltes Engineering im Netzwerk, sind dabei schlank zu verknüpfen.
Zusammenspiel aus Prozessbetrieb und Optimierungsberechnung
ArtiMinds bietet mit seiner Robot Programming Suite in Kombination mit der Learning & Analytics for Robots nicht nur für die No-Code- bzw. Low-Code-Roboterprogrammierung ein durchgängiges Softwarepaket. Beide Softwarelösungen sorgen gerade bei den beschriebenen Instandhaltungskonzepten für eine nahtlose Handhabung. Nachdem ein Roboterprogramm initial als nativer Code auf die Robotersteuerung gespielt wurde, können Teach-Punkte im nativen Programm auf die übliche Weise an der Anlage manuell nachjustiert werden. Zusätzlich hat der Werker die Möglichkeit, auch die beiden weiterführenden Methoden anzuwenden.
Für datengetriebene, automatische Korrekturen ermöglicht eine SPS bzw. die Anbindung der Robotersteuerung und der SPS über Netzwerk an einen Computer – ganz gleich ob direkt in der Anlage, in der Linie oder einem Rechenzentrum – das Zusammenspiel aus Prozessbetrieb und Optimierungsberechnung. Von der Robotersteuerung gelangen die Daten auf den Computer, der die Datenbank sowie zugehörige algorithmische Berechnungsmethodiken enthält. Dort werden laufend Korrekturen berechnet und anschließend, abgesichert durch die SPS, dem Roboterprogramm zur Verfügung gestellt.
Mit der Kombination aus händischen Anpassungen und datengetrieben automatischen Korrekturen an der Anlage sowie der Vorbereitung größerer Eingriffe im digitalen Zwilling können die verschiedenen Stärken der Methoden komplementär eingesetzt werden. Denn die automatische Korrektur spart Arbeitsaufwand und Stillstandzeit, kann jedoch nicht mit jeder Ausnahmesituation und auch nicht mit Änderungen der Programmlogik umgehen. Die schnell mit der realen Anlage synchronisierbare Vorbereitung am digitalen Zwilling verringert Stillstandzeit, unnötige Fehler, z.B. verursacht durch hohen Zeitdruck, und vermeidet lange unkomfortable Arbeit direkt an der Linie. Zusätzlich bleiben manuelle Anpassungen direkt an der Anlage weiterhin auf gewohnte Weise möglich, um punktuelle, ungewöhnliche Probleme zeitnah zu adressieren.